What is a Wiring Harness?
A wiring harness is an integrated transmission assembly composed of multiple conductors through precision braiding, standardized bundling, and specialized sleeving processes. It serves as the fundamental connectivity solution for modern electrical systems, comprising three core functional modules:
- Power transmission module: Utilizes multi-gauge conductors for energy delivery at various power levels
- Signal transmission module: Implements shielded conductors for control signals and data communication
- Structural protection module: Incorporates multiple protective materials to ensure system reliability
Table of Contents
1. Core Component Technical Specifications
1.1 Conductor Selection Standards
- Power conductors: 2-20mm² cross-section (automotive grade)
- Signal conductors: 0.22-0.5mm² fine-wire design
- Special environment conductors: High-temperature/corrosion-resistant materials
1.2 Protection System Configuration
- Basic protection: PVC insulating tape (0.15-0.3mm thickness)
- Intermediate protection: Flame-retardant corrugated tubing (-40℃~125℃ operating temp)
- Advanced protection: Metal braided shielding (≥60dB EMI protection)
1.3 Connector Systems
- Standardized interfaces: USCAR-2/20 series
- Modular design: ≥50 mating cycles
- Environmental sealing: IP67 protection rating
2. Engineering Design Principles
2.1 Electrical Performance Design
- Current capacity: Continuous current ≤60% of conductor rating
- Voltage drop control: Line drop ≤3% of nominal voltage
- Insulation performance: ≥20MΩ insulation resistance (500VDC test)
2.2 Mechanical Performance Requirements
- Automotive grade: ≥1 million flex cycles (-40℃~85℃)
- Industrial grade: Vibration resistance 10- 2000Hz at 15g
- Aerospace grade: Vacuum environment compatibility (10^-6Pa)
3. Typical Application Parameters
3.1 Automotive Wiring Systems
- Operating temperature range: -40℃~125℃
- Oil resistance: No degradation after 240h IRM903 oil immersion
- Minimum bend radius: ≥5× conductor diameter
3.2 Industrial Equipment Harnesses
- Flame rating: UL94 V-0
- Tensile strength: ≥50N/mm²
- EMI protection: Twisted pair + aluminum foil shielding
4. Quality Control Essentials
- Continuity testing: 100% inspection
- Insulation testing: 1500VAC/1min withstand
- Environmental testing: 100 temperature cycles (-40℃~125℃)
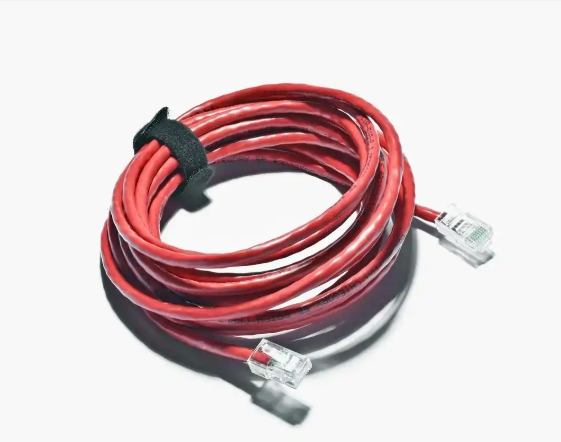
What Does a Wiring Harness Do?
Wiring harnesses are widely used in electronics, automotive, aerospace, and other industries where complex circuits require the integration of multiple wires or cables. By bundling and organizing these connections, wiring harnesses ensure compact, orderly, and efficient electrical systems.
Key Functions of a Wiring Harness
Wire Protection: Sleeving and insulation materials shield wires from environmental hazards such as moisture, chemicals, and abrasion.
Cable Management: Harnesses consolidate wires into structured layouts, minimizing clutter and simplifying installation or maintenance.
Signal Transmission: They serve as pathways for electrical signals between components, enabling system communication and control.
Power Distribution: Harnesses deliver electricity from power sources to devices, meeting energy demands across the system.
Design and Manufacturing Considerations
Wiring harnesses must adhere to electrical specifications (e.g., voltage, current, temperature) and select appropriate wires, connectors, and insulation based on application requirements. Their reliability is critical to system performance, necessitating strict quality control and testing during production.
How Do Wiring Harnesses Work?
A wiring harness is an integrated assembly of cables or wires designed to transmit power and signals. Its operation involves design, manufacturing, and testing processes, leveraging automated or semi-automated systems to ensure efficient and precise electrical connections.
1. Design & Parameter Analysis
- Layout Design: Based on the application (e.g., automotive, aerospace), the structure, dimensions, and materials are determined. For instance, automotive harnesses must account for varying current loads (continuous vs. intermittent duty cycles).
- Simulation: CAD software optimizes wire routing to prevent EMI or mechanical stress.
- Test Compatibility: Designs must align with testing standards (e.g., continuity, insulation resistance, dielectric strength).
2. Automated Manufacturing
- Cutting & Stripping: Automated machines precisely cut wires and strip insulation for consistent terminations.
- Crimping & Assembly: Non-standard presses or inserters attach terminals, with optional tinning for enhanced conductivity.
- Flexible Production: Custom automation supports rapid reconfiguration for small-batch orders.
3. Testing & Quality Control
- Continuity Test: Low-voltage checks for open/short circuits.
- 4-Wire Resistance Test: Eliminates contact resistance errors for accurate measurements.
- Hi-Pot Test: High-voltage verification of insulation integrity (e.g., 500V–1000V).
4. Industry-Specific Requirements
- Automotive: Must endure extreme temperatures/vibrations and handle dynamic loads (e.g., defrosters vs. AC systems).
- Aerospace: Demands zero-defect reliability, often requiring automated test systems (e.g., ATE harness testers).
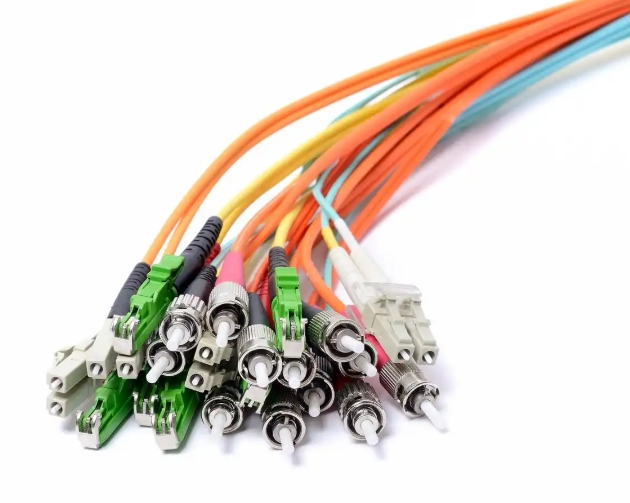
Application of Wiring Harnesses in PCBs
Wiring harnesses serve as critical interconnection components in PCB systems, with key applications in the following areas:
1. Connector System Design
In PCB layout, wiring harness connectors are essential for modular connectivity. The design process includes:
- Connector Selection and Placement: Choosing appropriate connector models based on signal type and current load
- Harness Network Configuration: Defining harness topology and signal paths using CAD software
- Interface Standardization: Implementing uniform harness entry designs to ensure compatibility and maintainability
2. Harness Type Selection
Three primary harness solutions are used depending on application requirements:
- Point-to-Point Harnesses: Simple and reliable structure, ideal for fixed-path multi-cable integration
- Branched Harnesses: Enable multi-directional routing from a single interface, optimizing space utilization
- FPC Flexible Harnesses: Ultra-thin design, particularly suitable for high-density installations
3. Protective Treatment Processes
Advanced protection technologies ensure PCB reliability in harsh environments:
- PUR 1680 Two-Component Potting Compound:
- Curing Methods: Supports both room-temperature and heat-activated curing
- Performance Characteristics: Excellent chemical resistance and moisture protection
- Mechanical Properties: Maintains optimal elasticity to relieve thermal stress
4. Soldering Process Control
Harness soldering is a critical PCBA manufacturing step requiring strict quality control:
- Common Failure Modes:
- Incorrect wire selection
- Assembly process defects
- Inadequate test coverage
- Quality Assurance Measures:
- Implementing incoming inspection protocols
- Establishing standardized operating procedures
- Developing comprehensive functional testing programs
Application Recommendations
For engineering applications, we recommend:
- Conducting thorough simulation verification during design phases
- Selecting certified harness components
- Implementing complete quality traceability systems
- Incorporating maintenance-friendly design features
Fundamental Differences Between Harnesses and Standard Cables
Structural Comparison
- Standard Cables:
▶ Single-layer insulation
▶ Single-conductor transmission
▶ Standard length supply - Wiring Harness Systems:
▶ Multi-layer protection (insulation + braiding + sheathing)
▶ Multifunctional integration (power + signal + data transmission)
▶ Custom topology design
Functional Evolution
Modern harnesses have evolved from simple power transmission to:
- Smart power distribution carriers
- Data communication media (e.g., automotive Ethernet harnesses)
- System diagnostic interfaces (with integrated fault detection circuits)
Application Differences
- Traditional Cables: Basic applications like lighting circuits
- Harness Systems:
▶ EV powertrain systems
▶ Industrial robot motion control
▶ Aircraft avionics interconnections
Wiring Harness Applications and Technical Advantages
Application Fields and Typical Scenarios
- Automotive Industry
- Serves as the vehicle’s “neural network system,” enabling efficient interconnection between ECUs, sensors, and actuators
- Key applications:
• High-voltage harnesses for NEVs (withstand 600V rating)
• Advanced driver-assistance system (ADAS) sensor harnesses
- Aerospace
- Utilizes MIL-STD-202G compliant high-reliability harnesses
- Critical applications:
• Flight control system harnesses
• Avionics interconnection harnesses
- Industrial Automation
- Solution: Modular harnesses enable rapid PLC-to-field device deployment
- Representative case: Robotic joint harnesses (>500,000 bending cycles)
- Consumer Electronics
- Micro FPC harness applications in smartphones and wearables
Core Competitive Advantages
Advantage | Technical Specification | Industry Benefit |
---|---|---|
Installation Efficiency | Pre-assembly saves 70% of labor hours | 35% production line efficiency gain |
System Reliability | IP67+ waterproof rating | 40% reduction in warranty failures |
Space Utilization | 3x higher wiring density | 25% equipment size reduction |
Maintenance | Modular quick-disconnect design | 60% shorter maintenance time |