Fasteners play a critical role in assembling and installing printed circuit boards (PCBs). This article provides a complete overview of common PCB fastener types, analyzes their unique advantages and functions, and offers solutions to frequently encountered application problems, helping engineers and technicians make more informed decisions.
Table of Contents
1. Overview of PCB Fasteners
PCB fasteners are indispensable mechanical connection components in electronic devices. They provide physical support and fixation and impact product reliability, durability, and production efficiency. As electronic devices trend toward miniaturization and higher density, requirements for PCB fasteners have become increasingly stringent. Understanding the characteristics, suitable applications, and potential issues of various fasteners is essential for designing reliable and durable electronic equipment.
2. Screws: The Core Component of PCB Connections
Screw Types and Characteristics
Screws are the most commonly used fasteners in PCB assembly, primarily categorized as follows:
- Phillips Head and Slotted Head Screws: Phillips head screws, with their self-centering feature, can improve assembly efficiency by 30% in automated production lines, making them the mainstream choice in consumer electronics. Slotted head screws are still used in certain special applications.
- Classification by Head Structure:
- Dome Head Cap Screws: Particularly suitable for areas requiring greater fastening force. M3/M4 specifications perform exceptionally well in applications needing over 5 N ·m of torque. Their deep drive design can withstand impacts from electric screwdrivers at 1200 rpm in production lines, preventing stripping.
- Countersunk Head Screws (e.g., GB/818 standard): Suitable for aluminum alloy panels with thickness ≤1.6mm, ensuring surface flatness errors within ±0.05mm after installation. Often used for secondary panels (cosmetic panels) in devices, providing a smooth and aesthetically pleasing surface.
- Pan Head Screws: A universal choice for most mechanical connections without special surface requirements.
- Hex Socket Head Screws: Offer higher torque transmission capability, commonly used in areas requiring high fastening force.
- Self-Tapping Screws (Thread-Cutting Screws): Used for metal plates, wooden boards, and similar materials, capable of creating their threads. For M2.5-M4 specifications on fiberglass epoxy substrates, installation torque should be controlled between 0.6- 1.2 N ·m to prevent substrate delamination.
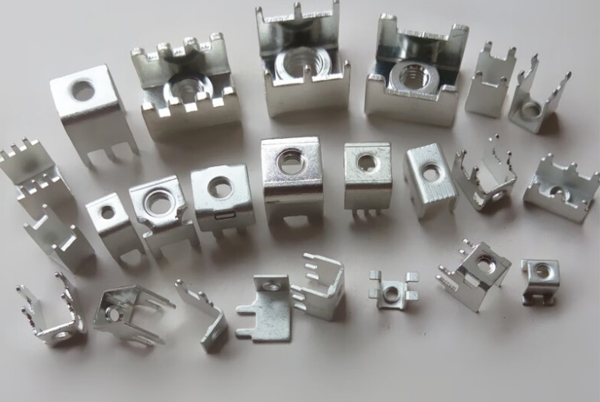
Screw Selection Guide
- General Applications: Prioritize cap screws or pan head screws, especially dome head cap screws, as their deep drives can withstand greater fastening force without damage.
- Flat Surface Requirements: Choose countersunk head screws to ensure the screw sits flush with the panel surface, achieving precise positioning and an attractive appearance. Note that countersunk screws have shallow drives and cannot withstand excessive fastening force.
- Thin Sheet Material Connections: Consider self-tapping screws to avoid pre-threading processes and improve assembly efficiency.
Common Screw Issues and Solutions
Q1: Why are cross-head screws recommended over slotted screws for PCB assembly?
A1: Cross-head screws offer self-centering advantages, improving assembly efficiency by 30% in automated production lines. The screwdriver is less likely to slip out, making it particularly suitable for the mass production of consumer electronics.
Q2: What applications are dome head cap screws best suited for?
A2: They are ideal for applications requiring higher fastening force. M3/M4 specifications perform exceptionally well when torque exceeds 5N·m, with their deep drive design capable of withstanding impacts from electric screwdrivers at 1200 rpm, effectively preventing stripping.
Q3: What precautions should be taken when using countersunk head screws?
A3: They are suitable for aluminum alloy panels ≤1.6mm thick, with post-installation surface flatness tolerance controlled within ±0.05mm. Due to their shallow drive, they shouldn’t be used where high fastening force is required, and are typically used for cosmetic panels.
Q4: How to prevent PCB delamination caused by self-tapping screws?
A4: Installation torque must be strictly controlled between 0.6- 1.2 N ·m. Consider switching to pre-threaded processes or adding reinforcement pads at screw locations to prevent fiberglass epoxy substrate delamination.
3. Nuts: Ensuring Secure Connections
Nut Types and Characteristics
- Traditional Nuts:
- Hex Nuts: The most universal type, suitable for most standard connections.
- Wing Nuts: Can be tightened manually without tools, ideal for frequently disassembled applications.
- Cap Nuts: Provide an aesthetically pleasing cover for thread ends while preventing injury from exposed threads.
- High-Performance Lock Nuts:
- Nylon Insert Lock Nuts (e.g., M3 specification): Utilize polymer friction damping to increase resonance loosening threshold from 15g to 28g, especially suitable for industrial environments with vibration frequencies >200Hz.
- All-Metal Lock Nuts: Feature a double-thread design, achieving zero loosening records over 10 years in 5G base station applications.
- SMT Nuts (Surface Mount Technology): Suitable for high-density assemblies. Peak soldering temperatures must be controlled at 260℃±5℃ to prevent cold solder joints.
Nut Selection Guide
- High-Vibration Environments: Prioritize nylon insert lock nuts or all-metal lock nuts.
- High Appearance Requirements: Consider cap nuts for both aesthetics and safety.
- Automated Production: SMT nuts can significantly improve production efficiency but require strict control of reflow soldering temperature profiles.
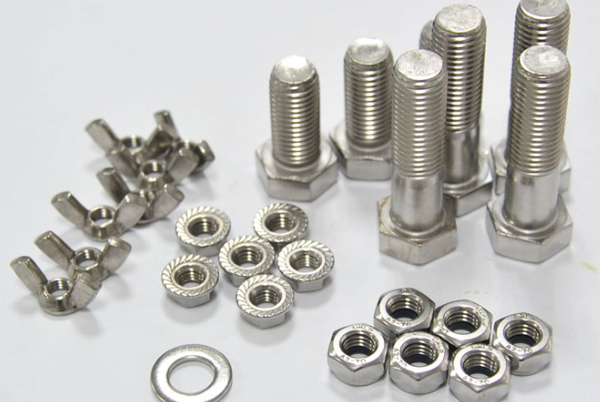
Common Nut Issues and Solutions
Q5: How to prevent nut loosening in high-vibration environments?
A5: For environments with vibration frequencies >200Hz:
- Use nylon insert lock nuts, which increase the loosening threshold from 15g to 28g through friction damping
- Employ all-metal lock nuts with a double-thread design
- Combine with lock washers
- Regularly check the tightness
Q6: What precautions are needed when soldering SMT nuts?
A6: Strict control of soldering parameters is essential:
- Peak temperature 260℃±5℃
- Optimized reflow soldering profile
- Proper solder paste selection
- Prevention of cold solder joints
Q7: How to select appropriate nuts for different applications?
A7:
- High vibration: Nylon insert or all-metal lock nuts
- Cosmetic requirements: Cap nuts
- Frequent disassembly: Wing nuts
- High-density assembly: SMT nuts
4. Washers: The Multifunctional Small Component
Washer Types and Characteristics
- Traditional Washers:
- Flat Washers: Distribute pressure and protect connected surfaces.
- Spring Lock Washers: Provide continuous spring force to prevent nut loosening.
- High-Performance Washers:
- Composite Lock Washers (Stainless Steel + Silicone): Maintain a friction coefficient above 0.8 in harsh environments ranging from -40℃ to 125℃.
- Conductive Washers (Gold-Plated Copper): Used in 5G millimeter-wave modules, with contact resistance <2mΩ, meeting 28 GHz signal transmission requirements.
- Thermal Expansion Compensation Washers (Shape Memory Alloy): Can reduce BGA package stress by 60% during temperature cycling.
Washer Selection Guide
- High Anti-Loosening Requirements: Choose spring lock washers or composite lock washers.
- High-Frequency Signal Applications: Consider conductive washers to ensure proper grounding and signal integrity.
- Large Temperature Variations: Thermal expansion compensation washers can effectively alleviate thermal stress.
Common Washer Issues and Solutions
Q8: How to select washers for wide temperature ranges?
A8: Stainless steel + silicone composite lock washers are recommended, maintaining a stable friction coefficient >0.8 in -40℃~125℃ environments, outperforming standard metal washers.
Q9: What special requirements exist for washers in high-frequency applications?
A9: For 5G millimeter-wave modules:
- Use gold-plated copper conductive washers
- Contact resistance must be <2mΩ
- Ensure 28GHz signal transmission quality
- Optimize placement to shorten grounding paths
Q10: How to address connection issues caused by thermal stress?
A10:
- Use shape memory alloy washers
- Design thermal expansion gaps
- Select materials with matching CTE
- Can reduce BGA package thermal stress by 60%
5. Clamps and Cable Ties
Clamp Types and Characteristics
- Standard Clamps: Provide basic fixation with diverse shapes and sizes.
- High-Performance Clamps:
- Two-Degree-of-Freedom Buffer Clamps: Feature conical springs between the base plate and sliding plate, absorbing over 20g of impact acceleration, suitable for high-vibration environments.
- Dynamic Load Distribution Clamps: Triangular rib layouts reduce PCB bending by 82%, excelling in applications like drone flight control boards.
- Carbon Fiber Clamps: Used in 5G base station AAU units, reducing weight by 40% while improving heat dissipation efficiency.
Cable Tie Types and Characteristics
- Standard Cable Ties: Secure wire positions, reducing movement and tension at electrical connections.
- High-Performance Cable Ties:
- Segmented Shield Cable Ties: Combine nickel-plated copper strips with ferrite in servo drives, reducing radiation noise by 12 dB.
- Impedance-Matched Cable Ties: RF cable tie dielectric constants must stay within ±10% of cable jacket values to ensure signal integrity.
- Creep Compensation Cable Ties: Use spring preload structures in new energy vehicle high-voltage wiring harnesses to accommodate 0.2mm/year copper deformation.
Clamp and Cable Tie Selection Guide
- High-Frequency Vibration Environments: Choose clamps with buffer structures, such as two-degree-of-freedom designs.
- RF Applications: Impedance-matched cable ties effectively maintain signal quality.
- High Long-Term Stability Requirements: Consider cable ties with creep compensation mechanisms.
Common Usage Issues and Solutions
Q11: How to minimize PCB warping after installation?
A11:
- Adopt a dynamic load distribution design
- Use triangular rib layout (reduces bending by 82%)
- Optimize clamp placement and quantity
- Select proper stiffness carbon fiber materials (40% weight reduction with improved heat dissipation)
Q12: What are the key technologies for high-frequency cable securing?
A12:
- Use dielectric-matched cable ties (±10%)
- Implement segmented shielding (nickel-plated copper + ferrite reduces noise by 12dB)
- Ensure impedance continuity
- Consider creep compensation (for 0.2mm/year deformation)
Q13: How to prevent long-term clamp loosening?
A13:
- Use two-degree-of-freedom buffer structures (absorbs >20g impact)
- Employ a spring preload design
- Regular maintenance checks
- Redundant fastening for critical areas
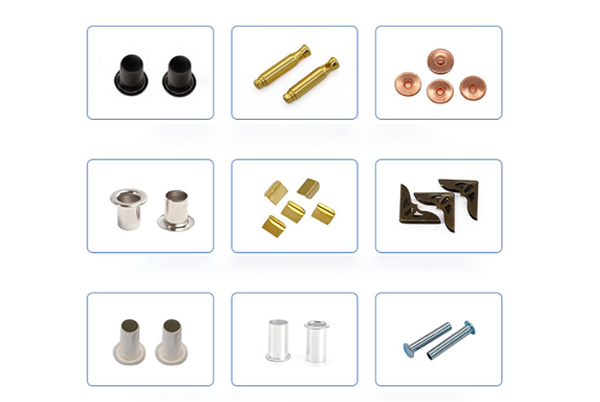
6. Comprehensive Fastener Selection Recommendations
- Consider Environmental Factors: Temperature, humidity, vibration frequency, and other environmental conditions directly impact fastener performance and lifespan. For example, in industrial environments with vibration frequencies >200Hz, traditional hex nuts have an annual failure rate of up to 12%, necessitating nylon insert lock nuts or all-metal lock nuts.
- Match Material Properties: Different materials vary significantly in expansion coefficients, conductivity, strength, and other characteristics. For instance, 5G millimeter-wave modules should use gold-plated copper conductive washers to ensure contact resistance <2mΩ.
- Optimize Installation Processes: Proper installation methods and tool selection are equally important. For example, SMT nuts require peak soldering temperatures controlled at 260℃±5℃ to prevent cold solder joints, while self-tapping screws on fiberglass epoxy substrates should be installed at 0.6-1.2N·m torque.
- Balance Cost and Performance: High-performance fasteners often come at a premium; make reasonable selections based on product positioning and reliability requirements. Consumer electronics may use standard Phillips head screws, while aerospace applications may require specialty alloy fasteners.
- Consider Maintenance Needs: For equipment requiring frequent maintenance, choose easily removable fasteners (e.g., wing nuts) to improve service efficiency.
7. Future Development Trends
PCB fastener technology continues to evolve, with major trends including:
- Smart Fasteners: Integrated sensors for real-time preload monitoring and predictive maintenance.
- Nanomaterial Applications: Nanocoatings to improve wear resistance and corrosion protection.
- Adaptive Structures: Automatic preload adjustment based on environmental changes (e.g., temperature).
- Greener Materials: Increasing use of recyclable and biodegradable materials.
- Higher Integration: Tighter integration with PCB manufacturing processes, such as embedded fastener structures.
Conclusion
Though small, PCB fasteners significantly impact the reliability, durability, and performance of electronic devices. By understanding the characteristics, advantages, and application techniques of various fasteners, engineers can make optimized choices for different scenarios, avoid common issues, and design more reliable and durable electronic products. As technology advances, PCB fasteners will continue to evolve, providing stronger, smarter connection solutions for electronic devices.