Flexible PCB (Printed Circuit Board) manufacturing is a specialized process that involves creating circuit boards with the ability to bend, twist, and conform to various shapes and applications. These flexible circuits offer a range of advantages over traditional rigid PCBs, making them suitable for applications where space, weight, and flexibility are critical factors. They are widely used in industries such as consumer electronics, automotive, aerospace, medical devices, and more.
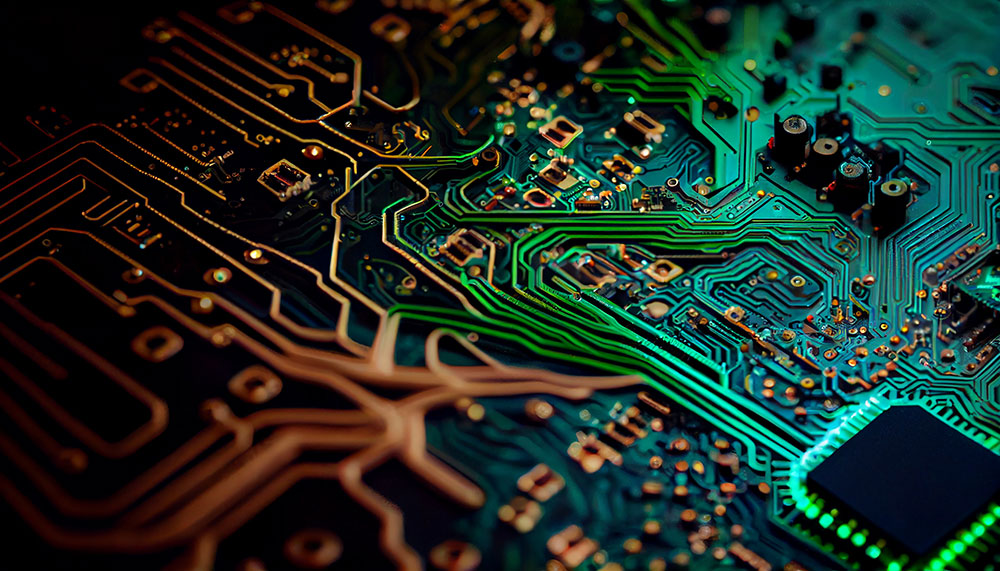
Table of Contents
Steps of flexible PCBs Manufacturing Process
- Design: The process starts with designing the circuit layout using specialized software. Designers need to consider factors such as the intended application, desired flexibility, and the arrangement of components.
- Substrate Material Selection: Flexible PCBs are typically constructed using flexible substrate materials such as polyimide (PI) or polyester (PET). These materials can withstand bending and twisting without compromising the integrity of the circuit.
- Lamination: The chosen substrate material is coated with a layer of conductive material, usually copper, using methods like sputtering, electroplating, or etching. This conductive layer forms the circuit traces and pads.
- Photo Imaging: A layer of photosensitive material, known as a photoresist, is applied over the conductive layer. A photomask with the circuit pattern is used to expose the photoresist to light, creating a stencil for the circuit pattern.
- Etching: The exposed copper is chemically etched away, leaving behind the desired circuit traces and pads. The unexposed photoresist is then removed, revealing the final conductive pattern.
- Drilling: If the flexible PCB requires components to be mounted on both sides, vias (holes with conductive material) are drilled through the substrate. These vias provide electrical connections between the different layers of the circuit.
- Plating and Surface Finish: The vias are plated to ensure reliable electrical connections between layers. Surface finishes, such as gold or tin, are applied to protect the exposed copper and enhance solderability.
- Component Attachment: Components are attached using techniques like surface mount technology (SMT) or through-hole mounting. SMT components are directly soldered onto the surface of the flexible PCB, while through-hole components are inserted through drilled holes and soldered on the opposite side.
- Testing and Inspection: Rigorous testing and inspection processes are carried out to ensure the integrity of the flexible PCB. This includes checking for connectivity, continuity, and any potential defects.
- Flexibility Enhancement: In some cases, additional layers like coverlays or solder mask can be added to protect the circuit and enhance its flexibility. These layers also provide insulation and protection against environmental factors.
- Final Inspection and Quality Control: Before the flexible PCBs are shipped to customers, a final inspection is conducted to identify any defects or issues that might affect their performance. Quality control measures help ensure that the manufactured PCBs meet industry standards and customer requirements.

Overall, flexible PCB manufacturing involves a combination of specialized materials, precise manufacturing techniques, and thorough quality control to produce circuit boards that can withstand bending and flexing while maintaining reliable functionality. This technology continues to evolve, enabling innovative designs in various industries.
Flexible PCB vs Rigid PCB
Flexible PCBs (Printed Circuit Boards) and rigid PCBs are two distinct types of circuit boards with different characteristics, applications, and advantages.
Structure and Flexibility
Flexible PCBs: As the name suggests, flexible PCBs are designed to be flexible and can bend, twist, and conform to various shapes. They are made from flexible substrate materials like polyimide (PI) or polyester (PET), which allows them to be used in applications where space constraints or dynamic movement is a concern.
Rigid PCBs: Rigid PCBs are made from solid, inflexible materials such as fiberglass-reinforced epoxy. They cannot bend or flex like flexible PCBs and are used in applications where the board needs to maintain a fixed shape.
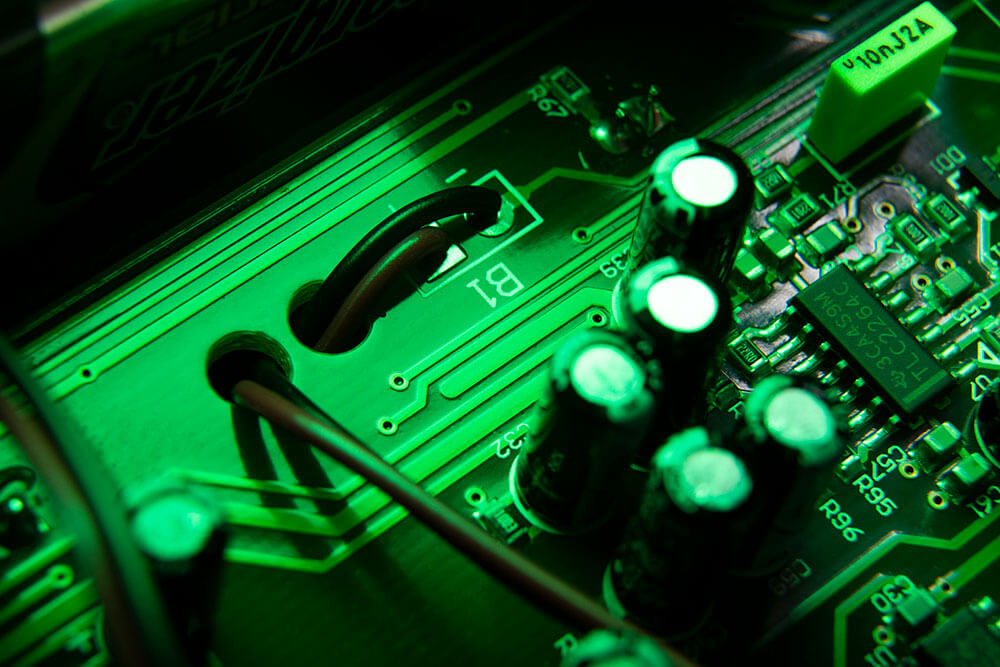
Applications
Flexible PCBs: These are ideal for applications that require compactness, lightweight design, and the ability to fit into unconventional spaces. They are commonly used in devices like wearable electronics, medical devices, aerospace equipment, and flexible displays.
Rigid PCBs: Rigid PCBs are suitable for most electronic devices, including computers, smartphones, home appliances, automotive electronics, and industrial equipment. They are used when a stable and sturdy platform is needed to house components and maintain a specific shape.
Space Efficiency
Flexible PCBs: Due to their flexibility and ability to be folded or molded, these PCBs can be designed to fit into tight spaces and irregular shapes, making them highly space-efficient.
Rigid PCBs: While they offer less flexibility, rigid PCBs can still be designed to be compact and space-efficient within their fixed dimensions.
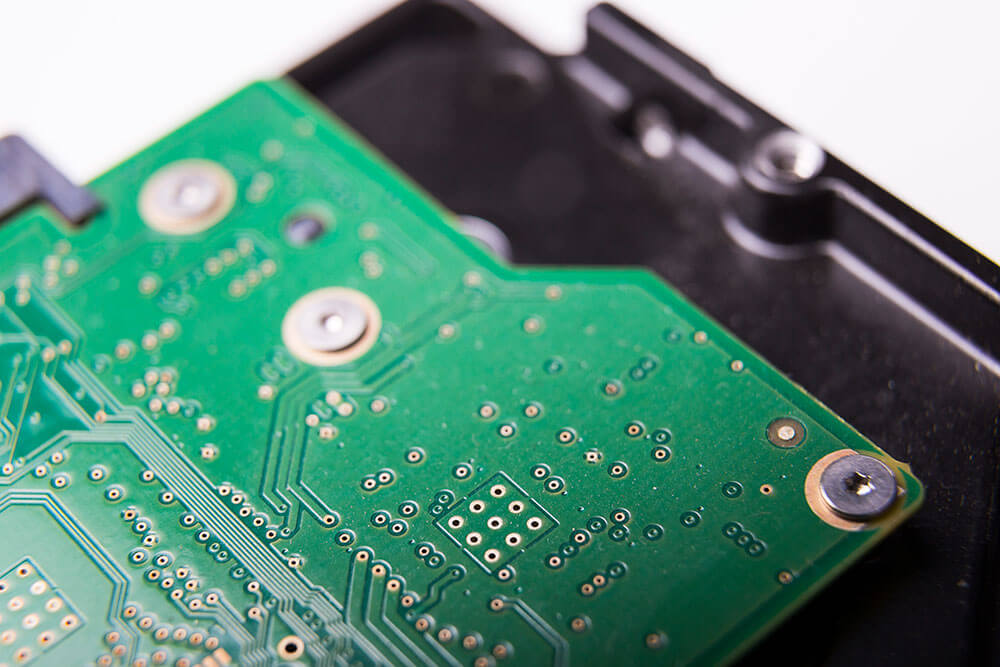
Weight
Flexible PCBs: The lightweight nature of flexible PCBs is advantageous in applications where weight is a critical factor, such as aerospace or wearable technology.
Rigid PCBs: These boards are generally heavier due to their solid construction, making them more suitable for applications where weight is less of a concern.
Design Complexity
Flexible PCBs: Designing flexible PCBs can be more challenging due to the need to accommodate bending and flexing while maintaining electrical integrity. The arrangement of components and routing of traces requires careful consideration to avoid stress on the materials.
Rigid PCBs: Rigid PCBs offer a simpler design process since the board’s shape remains constant. Components can be placed and routed more easily without the need to account for flexibility.
Cost
Flexible PCBs: The manufacturing process for flexible PCBs can be more complex, involving specialized materials and techniques. This can make them more expensive to produce compared to rigid PCBs.
Rigid PCBs: Rigid PCBs are generally more cost-effective to manufacture due to the established processes and materials used in their production.
In summary, the choice between flexible and rigid PCBs depends on the specific requirements of the application. Flexible PCBs are favored when flexibility, space efficiency, and unique shapes are essential, while rigid PCBs are preferred for applications that prioritize stability, cost-effectiveness, and conventional form factors.
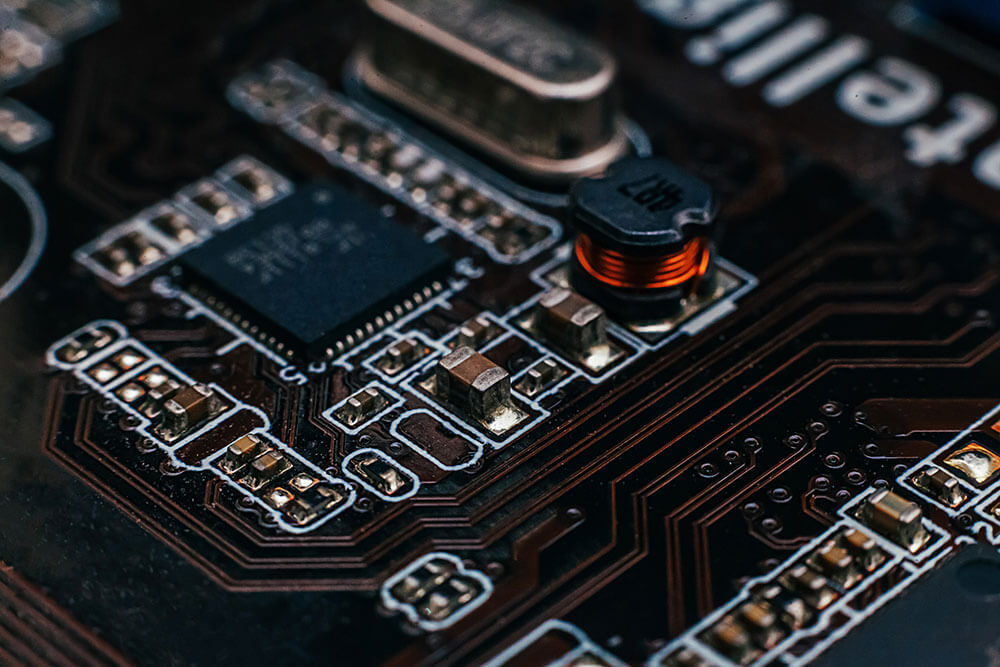
About Rigid-Flex PCB
Rigid-flex PCBs combine the advantages of both rigid and flexible PCBs into a single design, offering a solution for electronic devices that require a combination of flexibility and stability. Rigid-flex PCBs consist of both rigid and flexible sections, which are interconnected through special transition zones. This unique construction allows them to bend and flex while maintaining the structural integrity required for mounting components and ensuring reliable performance.
Rigid-flex PCBs are composed of alternating rigid and flexible layers. The rigid layers provide stability and support for components, while the flexible layers allow the board to bend, fold, or twist as needed. The transition zones between rigid and flexible sections are carefully designed to accommodate the mechanical stress during bending without compromising the electrical connections.
Manufacturing PCB with Topfast
Topfast PCB stands as a comprehensive solution for all PCB manufacturing needs. With expertise in producing Rigid PCBs, Flexible PCBs, and Rigid-flex PCBs, Topfast PCB showcases its commitment to catering to a wide spectrum of applications and industries. This diverse capability allows clients to harness the advantages of stability, flexibility, and hybrid designs, all under one roof. Topfast PCB’s proficiency in crafting high-quality circuit boards, whether rigid, flexible, or a combination of both, positions it as a reliable partner capable of delivering cutting-edge solutions tailored to the specific demands of each project.