Table of Contents
Common PCB Assembly Issues and Systematic Solutions
In the electronics manufacturing industry, PCB assembly quality directly impacts the performance and reliability of the final product. According to the latest IPC statistics, approximately 35% of early product failures stem from PCB assembly issues.
1. Soldering Defects
Soldering problems account for 42% of PCB assembly defects. The main types include:
- Cold Solder Joints
- Characteristics: Rough, dull solder surface
- Causes: Insufficient soldering temperature or time
- Solutions: Optimize reflow profiles to ensure peak temperatures meet solder paste specifications
- Insufficient Wetting
- Characteristics: Poor bonding between the component leads and pads
- Causes: Solder paste misalignment or oxidation
- Solutions: Regularly calibrate stencil printers and use nitrogen-protected soldering environments
- Solder Bridging
- Characteristics: Conductive connections between adjacent solder joints
- Causes: Excessive solder paste or insufficient component spacing
- Solutions: Optimize stencil aperture designs and implement step stencils to reduce solder volume
Expert Tip: Implement a Process Window Index (PWI) monitoring system to track key parameters like heating slope and liquidus time in real time.
2. Component Damage
Component damage during assembly often goes unnoticed but leads to early product failures:
- Pick-and-Place Machine Damage
- Excessive nozzle pressure cracks ceramic capacitors
- Solution: Set component-specific placement pressures
- Thermal Stress Damage
- BGA solder ball cracks due to CTE mismatch during reflow
- Solution: Use staged heating profiles with max ramp rates <3°C/s
- ESD Damage
- MOSFET degradation from electrostatic discharge
- Solution: Maintain ESD protection compliant with ANSI/ESD S20.20 standards
Inspection Methods: For hidden damage, use 3D X-ray and Scanning Acoustic Microscopy (SAM).
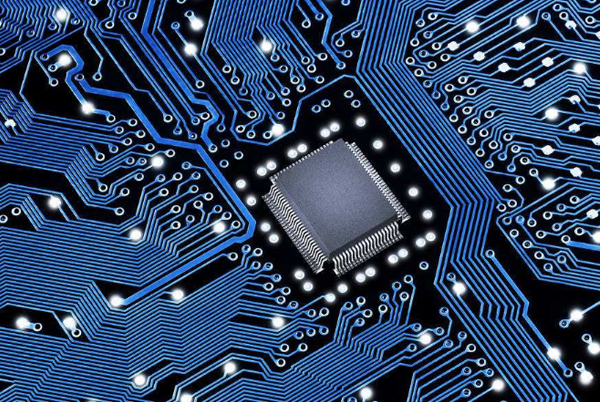
3. Short/Open Circuits
Systematic Short Circuit Solutions
- Design Phase Prevention
- Pad optimization: Replace circular pads with oval ones (30% spacing increase)
- Routing rules: Maintain 3x line width spacing for high-speed signals
- Power separation: >1mm spacing between voltage domains
- Production Process Control
- Control solder paste thickness (25-50 microns)
- Ensure solder mask dams >0.1mm
- Implement AOI for bridging defect detection
Targeted Open Circuit Measures
- Plating Issues
- Maintain through-hole copper thickness ≥25μm
- Use pulse plating for better hole wall coverage
- Soldering Defects
- Optimize solder paste activity (RMA or no-clean recommended)
- Ensure component lead coplanarity <0.1mm
Case Study: A telecom equipment manufacturer reduced short circuit defects from 850ppm to 120ppm through design rule optimization.
4. Pad Design Flaws: An Overlooked Critical Factor
- Incorrect Pad Sizing
- SMD pad length = component lead length + 0.5mm
- Pad width = 80-120% of lead width
- Poor Thermal Design
- Use thermal relief pads for high-power components
- Calculate thermal vias (2-3 x 0.3mm vias per 1A current)
- Solder Mask Issues
- Solder mask openings should exceed pads by 0.05-0.1mm
- Avoid narrow solder mask dams, causing bridges
Design Check: Use Valor NPI software for DFM analysis to detect issues early.
5. Multilayer PCB Challenges
- Drilling Quality
- Implement drill bit life management
- Optimize parameters: 1.5-3m/min feed rate, 80-120krpm speed
- Layer Misalignment
- Use Laser Direct Imaging (LDI) for better registration
- Add sufficient alignment targets (3-4 per side recommended)
- Inner Layer Shorts
- Control inner layer etch undercut (<20μm)
- Use AOI for inner layer inspection
Material Selection: Rogers 4350B for high-frequency applications, standard FR-4 Tg150°C otherwise.
6. Modern Inspection Technologies
- Traditional Method Comparison Method Capability Cost Speed AOI Surface defects Medium Fast X-ray Hidden joints High Slow Flying Probe Electrical tests Medium Medium
- Emerging Technologies
- AI-powered optical inspection: >98% defect detection accuracy
- Nano-impedance analysis: Detects micro-shorts
- Smart thermography: Predicts risk points pre-power
Investment Advice: For HDI PCBs, deploy integrated 3D SPI + X-ray + AOI inspection systems.
7. Environment and Operations
- Facility Requirements
- Temperature 23±2°C, humidity 45±5% RH
- Cleanliness: ISO 14644-1 Class 8
- Operational Standards
- IPC-A-610 certified operators
- Comprehensive ESD protection
- 5S workplace organization
- Material Management
- Refrigerate solder paste (0-10°C), 4-hour reflow before use
- Use opened PCBs within 72 hours
Success Story: An automotive electronics manufacturer reduced soldering defects by 60% through environmental improvements.
Recommendation
To systematically address PCB assembly issues:
- Design Phase
- Follow IPC standards
- Conduct a thorough DFM analysis
- Use verified component libraries
- Production Phase
- Establish strict process control points
- Implement SPC monitoring
- Deploy appropriate inspection equipment
- Personnel Management
- Regular technical training
- Quality accountability systems
- Encourage a defect reporting culture
For critical products, conduct reliability testing (thermal cycling, vibration tests, etc.). With systematic prevention and control, PCB assembly defect rates can be consistently maintained below 100ppm.