With the accelerating global aging population, the demand for medical electronic devices continues to grow, making PCB assembly technology increasingly vital in this field. As a core component of medical equipment, PCB assembly technology not only ensures the stable operation of existing medical devices but also drives innovation in medical electronics.
Five Core Values of Medical Electronics PCB Assembly
- Fundamental Functional Platform
- Serves as the signal processing hub for medical devices
- Typical applications:
- Signal acquisition and processing in medical imaging equipment (CT, MRI)
- Real-time data processing in vital signs monitors (ECG, EEG)
- Precision control in therapeutic devices (defibrillators, ventilators)
- Key Enabler of Miniaturization
- Achieves 20% volume reduction using HDI (High-Density Interconnect) technology
- Application cases:
- Non-invasive glucose monitors: Integrated 10-layer flexible PCBs
- Portable ultrasound devices: Miniaturized probe control circuits
- Implantable devices: Biocompatible ultra-thin PCB designs
- Core Carrier for Intelligent Upgrades
- Integrates multi-sensor fusion systems
- Representative smart medical solutions:
- Smart infusion systems: Combining flow/pressure/temperature sensing
- Remote monitoring devices: Supporting 5G/Wi-Fi dual-mode communication
- AI-assisted diagnostic equipment: Equipped with high-performance edge computing modules
- Reliability Assurance System
- Complies with medical-grade standards:
- IPC-A-610 Class 3 reliability standards
- Biocompatibility certification (ISO 10993)
- 96-hour continuous aging tests
- Critical process controls:
- Medical-grade lead-free soldering
- Conformal coating (anti-moisture/mold/salt spray)
- 100% AOI + flying probe testing
- Innovation Accelerator
- Rapid prototyping capabilities:
- 2-week turnaround from design to prototype
- Supports verification of 10+ specialty materials
- Emerging field applications:
- Wearable medical: Flexible, stretchable circuits
- Surgical robots: High-speed precision control boards
- Neural stimulators: Miniaturized implantable circuits
Technological Development Trends
- Material Innovation Directions
- Biodegradable substrate materials
- Antimicrobial surface treatments
- High-temperature/pressure-resistant specialty materials
- Process Breakthrough Focus Areas
- 01005 ultra-miniature component placement
- 3D printed circuit technology
- Irregular-shaped assembly solutions
- Intelligent Development Pathways
- Embedded AI chip integration
- Multi-modal data fusion processing
- Wireless power transmission technology
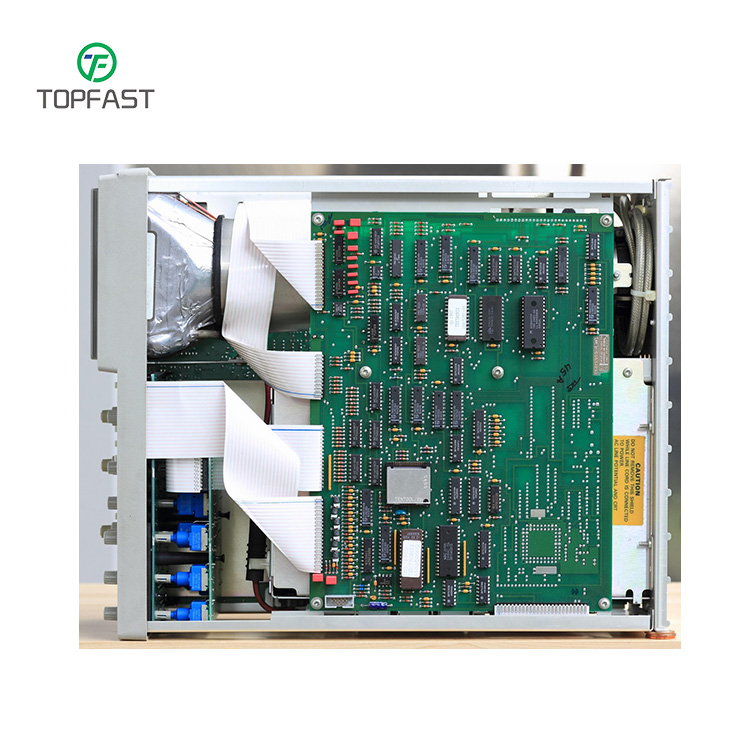
As a key enabling technology for medical electronics innovation, PCB assembly is evolving toward higher integration, better biocompatibility, and enhanced intelligence. Looking ahead, with the integration of 5G, AI, and other emerging technologies, medical electronics PCB assembly will embrace broader development opportunities, providing robust technical support for precision medicine and smart healthcare.
The Critical Role of PCBA in Modern Medical Devices
In this era of rapid technological advancement, medical devices play an increasingly vital role in safeguarding human health. At the heart of these devices lies the PCBA (Printed Circuit Board Assembly), whose quality directly impacts equipment performance and reliability. For procurement professionals in the electronics industry, a deep understanding of medical PCBA manufacturing processes is essential.
Table of Contents
Key Processes and Requirements in Medical PCBA Manufacturing
1. Functional Requirements and Layout Design
Medical devices demand complex, multifunctional PCBA designs. Engineers must carefully plan board dimensions, layer counts, and component placement while considering:
- Electrical performance
- Thermal management
- EMI/EMC compliance
- Manufacturing feasibility
Advanced circuit design software ensures optimal performance and production efficiency.
2. Material Selection and Quality Control
Medical-grade materials must meet stringent industry standards for:
- High-temperature resistance
- Corrosion protection
- Non-toxicity
All substrates, components, and solder paste undergo rigorous inspection to ensure safety and reliability.
Precision Manufacturing of Medical PCBs
1. High-Accuracy Fabrication Processes
PCB manufacturing involves:
- Precision cutting and drilling (±0.05mm tolerance)
- Copper plating and etching
- Photolithography
State-of-the-art equipment and strict process controls prevent defects that could compromise SMT assembly.
2. Controlled Production Environment
- Cleanrooms (Class 1000 or better)
- ESD-protected zones
- Temperature/humidity monitoring
3. SMT Assembly: Precision and Speed
- Placement accuracy: ≤0.1mm
- High-speed chip shooters (50,000+ CPH)
- Vision-aligned component mounting
4. Solder Paste Printing
- Laser-cut stencils (5-8μm thickness control)
- 3D SPI (Solder Paste Inspection) pre-reflow
5. Reflow Soldering
- Multi-zone profiling (ramp rates 1-3°C/sec)
- Nitrogen atmosphere (O₂ <500ppm)
- Void control <15% (X-ray verified)
6. Automated Optical Inspection (AOI)
- 3D AOI with 10μm resolution
- Defect detection rate >99.7%
7. Through-Hole (DIP) Assembly
- Wave soldering with selective pallets
- Rework stations for critical joints
Testing and Validation
1. Comprehensive Testing Protocols
- ICT: Continuity and component verification
- FCT: Full functional validation
- Burn-in Testing: 48- 96 hours at elevated temps
2. Debugging and Programming
- Firmware flashing for MCUs/FPGAs
- Signal integrity verification
Post-Assembly Processing
1. Cleaning and Coating
- Solvent cleaning (IPA/VOC-free)
- Conformal coating (IPC-CC-830B)
2. Packaging and Logistics
- Moisture-barrier bags with desiccants
- Shock/vibration testing for shipping
Conclusion
Medical PCBA manufacturing integrates over 20 precision processes, each requiring exacting standards (IPC-A-610 Class 3). As medical electronics evolve—incorporating AI, 5G, and IoMT—PCBA technology must advance in tandem. For procurement specialists, mastering these technical nuances ensures supply chain resilience and competitive advantage in this life-critical industry.
The future of healthcare electronics starts with perfection at the PCBA level.