PCBA (Printed Circuit Board Assembly) refers to the complete manufacturing process of precisely assembling various electronic components onto bare PCB boards. This critical process transforms basic circuit boards into fully functional electronic modules, representing the core of modern electronic device manufacturing.
Table of Contents
Key Processes in PCBA Electronics Manufacturing
- Precise component placement according to circuit designs
- Reliable connections through advanced soldering techniques
- Functional integrity assurance via rigorous testing
The central role of PCBA in electronic systems
- Signal transmission management: Establishing optimized electrical pathways
- Circuit implementation: Accurately realizing schematic designs
- Power integrity: Providing stable power distribution networks
- Impedance control: Ensuring high-frequency signal transmission quality
Key Factors Affecting PCBA Performance
✓ Component selection and quality
✓ Assembly process precision (±0.05mm placement tolerance)
✓ Solder joint reliability (IPC-A-610 compliant)
✓ Test coverage (≥95%)
PCBA Core Components
1. Foundation Substrate – PCB
- Multilayer composite structure (FR4/high-frequency materials)
- Key features:
- Mechanical support platform
- Electrical interconnection network
- Thermal management medium
2. Functional Units – Electronic Components
- Passive components: 0402/0201 package resistors/capacitors
- Active devices: QFN/BGA packaged ICs
- Electromechanical components: Connectors/switches
3. Interconnection System
- Precision traces: 3/3mil line width/spacing
- Interlayer connections: Laser blind/buried via technology
4. Connection Medium – Solder
- Composition: SAC305 lead-free alloy
- Process: Stencil printing (0.1-0.15mm thickness)
- Function: Forming reliable electrical-mechanical connections
Modern PCBA technology has evolved into a systems engineering discipline integrating materials science, precision mechanics, and electronics. Its quality directly determines end-product performance and reliability. As electronic devices trend toward miniaturization and high-frequency applications, PCBA processes continue advancing with HDI (High Density Interconnect) and 3D stacking technologies.
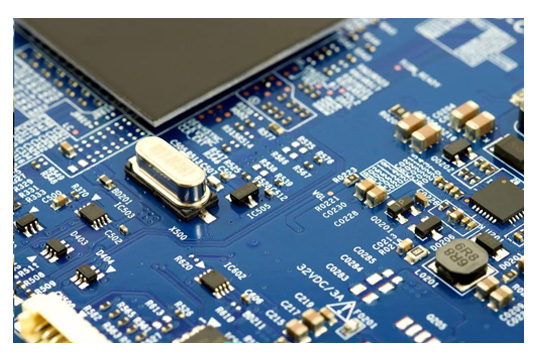
PCB is a mainstream assembly technology
1. Through-Hole Technology (THT)
Traditional assembly solution with distinctive features:
- Utilizes axial/radial lead components
- Mechanical fixation via PCB plated through-holes
- Dual-sided electrical connections formed by wave soldering
- Excellent mechanical strength and vibration resistance
Typical applications:
✓ Aerospace control systems
✓ Military electronic equipment
✓ Industrial-grade power electronics
✓ High-reliability instrumentation
Standard process flow:
① Precision drilling (hole diameter tolerance ±0.05mm)
② Component insertion (manual/auto-insertion)
③ Wave soldering (solder temperature 265±5°C)
④ Lead trimming and cleaning (IPC-7711 compliant)
2. Surface Mount Technology (SMT)
Modern high-density assembly solution with core advantages:
- Leadless component packages (0201 to BGA)
- Single/double-sided mounting capability
- Reflow soldering creates micro-metallurgical bonds
- Supports 0.4mm fine-pitch components
Typical applications:
✓ Consumer mobile devices
✓ IoT equipment
✓ Miniaturized medical electronics
✓ High-frequency communication modules
Standard process flow:
① Stencil printing (solder paste thickness 0.1-0.15mm)
② High-speed placement (±0.025mm accuracy)
③ Multi-zone reflow (peak temperature 235-245°C)
④ AOI inspection (≥99.9% defect detection rate)
Technology selection guidelines:
- THT recommended for high-reliability requirements
- SMT is essential for miniaturized designs
- Mixed technology (SMT+THT) for complex modules
- SMT+wire bonding preferred for RF circuits
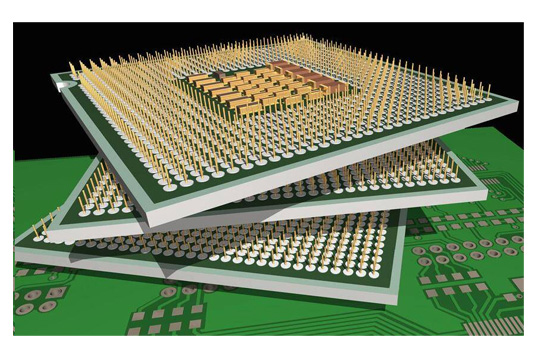
PCBA Testing: Ensuring Quality and Reliability
PCBA (Printed Circuit Board Assembly) testing is a critical phase in the manufacturing process, verifying that assembled boards meet quality standards and perform as intended. This comprehensive validation process examines multiple parameters, including IC programming, power characteristics, current/voltage measurements, and circuit continuity.
The Critical Role of PCBA Testing:
- Primary quality assurance checkpoint
- Guarantees functional performance and long-term reliability
- Prevents defective products from reaching end-users
- Reduces field failures and warranty claims
Comprehensive PCBA Test Methodologies:
- In-Circuit Test (ICT)
- Validates circuit functionality
- Measures precise current/voltage parameters
- Analyzes waveform characteristics (frequency, amplitude, noise)
- Typical fault detection rate: >99% for manufacturing defects
- Functional Circuit Test (FCT)
- Simulates actual operating conditions
- Identifies hardware/software integration issues
- Verifies full product functionality
- Includes burn-in testing for critical applications
- Flying Probe Test
- Utilizes movable probes for electrical verification
- Checks component values and characteristics
- Ideal for:
- Prototype validation
- Low-volume production
- High-mix environments
- Environmental Stress Testing
- Extreme condition evaluation:
- Thermal cycling (-40°C to +125°C)
- Humidity exposure (85% RH)
- Mechanical shock/vibration (per MIL-STD-883)
- IP rating validation for waterproofing
- Accelerated life testing methodology
Advanced Defect Detection:
Modern PCBA manufacturing employs automated optical inspection (AOI) and X-ray systems to identify:
- Component absence/misplacement
- Solder defects (bridges, insufficient solder)
- Placement accuracy (≤0.1mm tolerance)
- BGA voiding (<25% acceptable)
Test Strategy Selection Criteria:
Factor | High-Volume Production | Prototyping/Low-Volume |
---|---|---|
Optimal Test | ICT + AOI | Flying Probe + FCT |
Setup Time | 4-8 hours | <1 hour |
Cost Basis | NRE amortization | Minimal tooling |
Fault Coverage | >99% | 90-95% |
Implementation Best Practices:
- Develop a test coverage matrix during the DFM phase
- Implement graduated test severity for different product classes
- Combine automated testing with manual verification for critical assemblies
- Maintain comprehensive test data analytics for continuous improvement
This rigorous testing approach ensures delivered PCBAs meet IPC-A-610 Class 3 standards for high-reliability applications, while Class 2 commercial products maintain an appropriate cost-quality balance. Experienced manufacturers optimize test strategies based on production volume, complexity, and application requirements to deliver guaranteed quality outcomes.
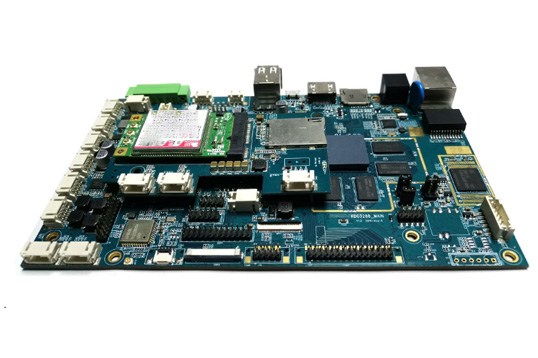
PCBA Cost Analysis
Understanding PCBA Cost Structure
The total cost of Printed Circuit Board Assembly involves multiple variables that require careful consideration:
Primary Cost Drivers:
- Labor & Automation Costs
- Varies by geographic region (Asia: $15-35/hr, North America: $50-120/hr)
- Automation level affects pricing (SMT lines typically 30-50% more efficient than manual)
- Technical Requirements
- SMT vs Through-Hole (THT) assembly
- Board complexity (2-layer vs 8-layer: 2- 5x cost difference)
- Component density (components/cm²)
- Volume & Lead Time Economics Quantity Price/Unit Lead Time Prototype (1-5) 5-8x 5-10 days Small Batch (50) 2-3x 10-15 days Mass Production (1k+) 1x 20-30 days
- Additional Considerations
- Component procurement (20-60% of total cost)
- Testing requirements (ICT adds 15-25%)
- Certifications (ISO 9001, IPC Class 3 compliance)
Strategic Manufacturer Selection Guide
1. Capability Assessment
- Verify equipment specifications:
- SMT placement accuracy (≤0.025mm)
- Maximum board size capacity
- Component handling range (01005 to large connectors)
2. Quality Assurance Protocol
- Required certifications:
- IPC-A-610 acceptance standards
- ISO 13485 for medical devices
- IATF 16949 for automotive
3. Design for Manufacturing (DFM)
- Critical evaluation points:
- Panelization efficiency
- Thermal management considerations
- Test point accessibility
4. Prototyping Best Practices
- Recommended workflow:
- Design verification (3-5 engineering samples)
- Design for Test (DFT) implementation
- Pilot run (50-100 units)
- Full-scale production
Cost Optimization Strategies:
- Standardize component packages
- Optimize panel utilization
- Implement automated optical inspection (AOI)
- Consolidate orders for volume discounts
Red Flag Warning Signs:
- Lack of proper documentation
- No engineering change order (ECO) process
- Inadequate ESD protection measures
- Limited material traceability
Selecting the right PCBA partner requires balancing technical capabilities, quality systems, and cost efficiency. Reputable manufacturers will provide transparent cost breakdowns and detailed DFM feedback before production begins.