Table of Contents
Here are the translations of the 8 PCB professional terms:
01 Panel (Array)
Some PCB manufacturers refer to arrays as “Panels.” Panels are divided into shipping panels and working panels. A shipping panel refers to the arrayed PCBs for shipment, usually designed to meet PCBA production requirements, and is sometimes called a “set.” A working panel refers to the production array, which contains multiple shipping panels. PCBs are manufactured as working panels and later separated into shipping panels.
02 Black Oxide / Brown Oxide
This is a chemical process that forms a uniform, fuzzy layer on the copper surface. This layer increases the contact area between the copper and prepreg (PP), enhancing adhesion.
The purpose of black oxide and brown oxide is the same, but they differ in the length of the fuzz, chemical cost, and process difficulty. Black oxide provides stronger adhesion than brown oxide, but it is more expensive and harder to manage. Additionally, black oxide is more prone to “pink ring” defects. Currently, most manufacturers use the brown oxide process.
03 Lamination
Multilayer PCBs require stacking multiple cores, PP layers, and copper foils, which are then bonded together under high temperature and pressure. Under heat, the PP becomes viscous and flows under pressure, filling the etched gaps in the inner copper layers.
04 Various Types of Holes
- PTH (Plated Through Hole): A copper-plated, metallized hole.
- NPTH (Non-Plated Through Hole): A non-copper-plated, non-metallized hole.
- Via: A small copper-plated hole used only for electrical conduction.
- Blind Hole: A hole that starts from the top or bottom layer but does not go through the entire board (visible on one side).
- Buried Via: A hole connecting inner PCB layers without reaching the outer copper layers (invisible from the outside).
- HDI (High-Density Interconnect) Hole: Micro-blind holes formed by laser drilling.
05 Electroless Copper Deposition (Chemical Copper Plating)
Also known as chemical copper plating, this process involves an oxidation-reduction reaction on the substrate surface to form a thin copper layer, enabling interlayer electrical connections and facilitating subsequent copper plating.
06 Solder Mask
The solder mask, also called solder resist, is a layer of ink applied to the PCB surface to prevent soldering shorts.
Solder mask ink is very common in PCBs, with about 90% being green. However, other colors are also available, such as red, blue, black, white, and yellow.
The functions of the solder mask include: - Preventing incorrect soldering of components.
- Preventing solder bridging.
- Providing protection (the polymer layer covers the metal traces, offering resistance to salt spray, moisture, etc.).
07 Surface Finish
Bare copper has good solderability but tends to oxidize when exposed to air for long periods. Therefore, surface treatment is applied to ensure good solderability or electrical performance.
Common surface finishes include: - HASL (Hot Air Solder Leveling)
- ENIG (Electroless Nickel Immersion Gold)
- OSP (Organic Solderability Preservative)
- Immersion Tin
- Immersion Silver
- Electroplated Gold
- Electroplated Gold Fingers
08 V-CUT
V-CUT is a common method for separating PCBs into individual units and removing waste edges. The remaining thickness after V-CUT refers to the thickness left after the upper and lower blades cut the PCB. This thickness must be neither too thick nor too thin—if too thick, separation is difficult and causes high stress; if too thin, the board lacks support and may break during production. Common V-CUT angles are 30°, 45°, and 60°.
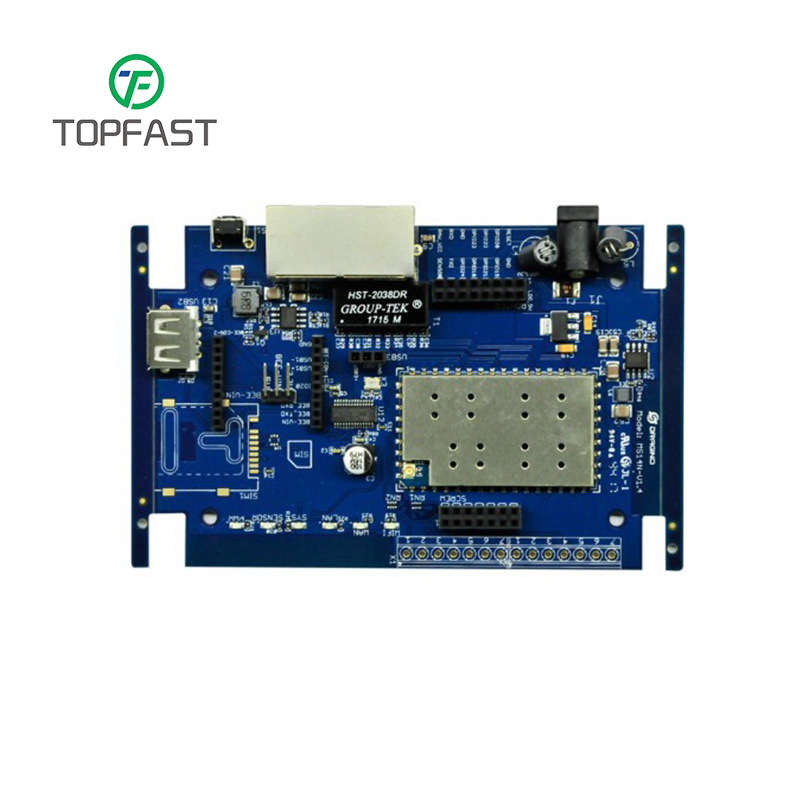
PCBA Processing – 30 Key Terms
In electronics manufacturing, PCBA (Printed Circuit Board Assembly) processing is a complex and precise process involving numerous technical terms and core technologies.
- PCBA – Short for Printed Circuit Board Assembly, referring to the entire process of PCB fabrication, including SMT assembly, DIP insertion, functional testing, and final assembly.
- PCB – Short for Printed Circuit Board, typically referring to circuit boards, which can be single-sided, double-sided, or multilayer, made from materials like FR-4, resin, fiberglass, or aluminum substrates.
- Gerber File – A set of files describing PCB images (circuit layers, solder mask, silkscreen, etc.) along with drilling and milling data, required for PCBA quotations.
- BOM (Bill of Materials) – A list of all components used in PCBA, including quantities and process routes, serving as a key reference for procurement.
- SMT (Surface Mount Technology) – A process involving solder paste printing, component placement, and reflow soldering on PCBs.
- Solder Paste Printing – Depositing solder paste through a stencil onto PCB pads using a squeegee blade.
- SPI (Solder Paste Inspection) – A machine that checks solder paste thickness and printing quality post-application.
- Reflow Soldering – Heating PCBs in a reflow oven to melt solder paste, forming solid solder joints upon cooling.
- AOI (Automated Optical Inspection) – A scanning system that detects soldering defects by comparing PCB images to standards.
- DIP (Dual In-line Package) – A process where through-hole components are inserted into PCBs, followed by wave soldering, pin trimming, touch-up, and cleaning.
- Wave Soldering – Passing PCBs over a molten solder wave to solder through-hole components.
- Pin Trimming – Cutting excess component leads after soldering for proper sizing.
- Touch-Up (Rework) – Repairing incomplete or defective solder joints manually.
- Board Cleaning – Removing flux residues and contaminants to meet environmental and cleanliness standards.
- Conformal Coating – Applying a protective layer (e.g., acrylic, silicone) to PCBA for insulation, moisture resistance, and corrosion prevention.
- Pads (Land Patterns) – Exposed copper areas on PCBs for component soldering.
- Component Packaging – The physical form of components, mainly DIP (through-hole) and SMD (surface-mount).
- Pitch (Lead Spacing) – The distance between adjacent component leads/terminals.
- QFP (Quad Flat Package) – A surface-mount IC with gull-wing leads on all four sides.
- BGA (Ball Grid Array) – An IC package with solder balls arranged in a grid on its underside.
- QA (Quality Assurance) – Ensures product quality through inspections and testing.
- FCT (Functional Circuit Test) – Simulates real-world operation to verify PCBA functionality.
- Burn-In Testing – Stress-testing PCBAs under extreme conditions to identify early failures.
- Vibration Testing – Assessing PCBA durability against mechanical vibrations during use/transport.
- IQC (Incoming Quality Control) – Inspects raw materials/components upon receipt.
- Stencil (Solder Mask) – A laser-cut metal sheet for precise solder paste deposition.
- Fixture (Jig) – A tool for batch production, including assembly, testing, and PCB test fixtures.
- Plated Through-Hole (PTH) – Copper-plated holes for interlayer connections/signal transmission.
- Solder Mask – A protective layer over copper traces to prevent shorts/corrosion.
- SMD (Surface-Mount Device) – Components mounted directly onto PCBs without leads, the dominant assembly method today.