Small-Batch PCB Production: Bridging Prototyping and Mass Production
In the electronics development process, small-batch PCB production faces the unique challenge of meeting rapid prototyping needs while preparing for mass production. This requires manufacturers to have both quick response capabilities and a rigorous quality control system.
Table of Contents
Rapid Prototyping Support System
- Design Optimization Service
- Experienced engineering teams complete DFM (Design for Manufacturability) analysis within 24 hours
- Specialized recommendations for HDI boards, high-frequency boards, and other complex designs
- Smart Inventory Management
- 2,000+ commonly used components and 30+ substrate materials in stock
- 90% of quick-turn prototype orders can be prepared within 72 hours
- Flexible Production Line
- High-precision laser drilling (±15μm), multi-zone reflow soldering, and other advanced equipment
- Supports small-batch production (1- 50 pcs) with fast turnaround
Mass Production Readiness
- Process Standardization
- 200+ process specifications (e.g., drilling spindle speed: 120- 150krpm, hole wall roughness ≤25μm)
- Equipment Maintenance
- Daily checks + quarterly overhauls for critical machines (OEE maintained at ≥95%)
- Quality Traceability
- MES system records key parameters for every batch, ensuring full product traceability
Three-Tier Quality Control
- Incoming Inspection
- 100% functional testing for critical components
- In-Process Inspection
- 28 quality checkpoints with first-article inspection + periodic sampling
- Final Inspection
- 100% electrical continuity testing
- Full visual inspection under 10x magnification
- Reliability testing (e.g., thermal cycling: -40℃~125℃)
Performance Metrics
✓ 5-day average lead time for prototypes
✓ First-pass yield ≥98.5%
✓ Smooth transition to mass production (success rate >90%)
This small-batch production model not only accelerates R&D iterations but also establishes a solid foundation for mass production, serving as a critical bridge between product development and market launch.
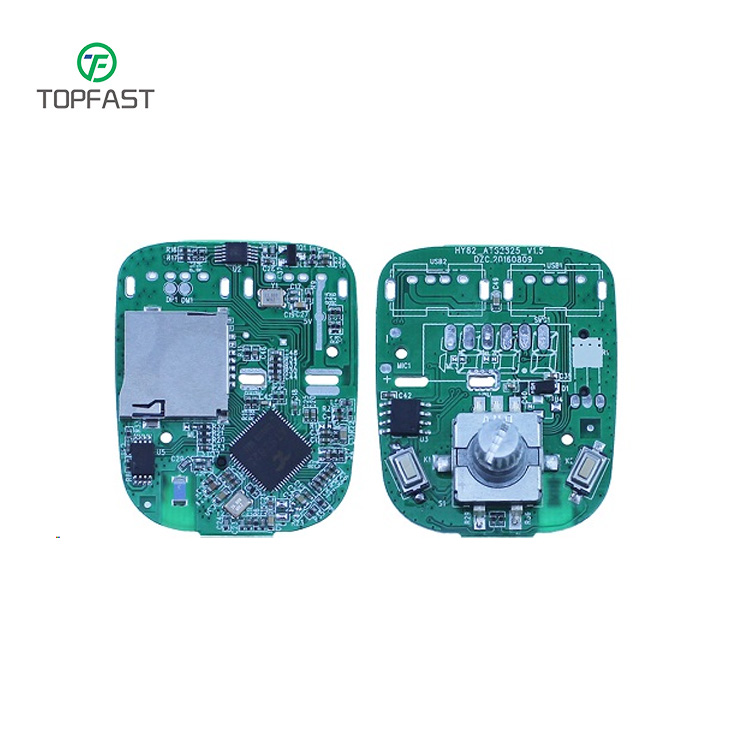
Key Success Factors for Small-Batch PCB Assembly
- Design Optimization Strategy
- Implement standardized component library management, prioritizing 0603 or larger package sizes
- Adopt modular design concepts to improve assembly efficiency by over 30%
- Optimize panelization designs to enable multi-variant PCB production
- Smart Procurement Solutions
- Establish Preferred Parts List (PPL) covering 2000+ standard components
- Develop an intelligent procurement platform for automatic multi-project demand consolidation
- Provide alternative component decision trees to ensure supply chain continuity
- Advanced Manufacturing Technology Application
- Configure high-flexibility SMT lines supporting quick changeover (<15 minutes)
- Deploy the MES system for full-process digital control
- Utilize selective 3D printing for specialized tooling and fixtures
- Efficient Testing Solutions
- Develop modular test platforms with an 85% adaptability rate
- Achieve a 90% automation rate for critical test procedures
- Implement a tiered testing strategy to optimize test coverage
- Manufacturer Selection Criteria
- Verify small-batch production track record (<100pcs cases)
- Evaluate equipment flexibility (minimum lot size capability)
- Establish a weekly project progress synchronization mechanism
Implementation Results:
✓ Prototype delivery cycle shortened by 40%
✓ Material costs reduced by 25%
✓ First-pass yield increased to 95% +
✓ Mass production transition period compressed by 50%
This solution is particularly suitable for:
- Automotive electronics prototyping
- Medical device small-batch trial production
- Industrial control equipment rapid iteration
By systematically implementing these five strategies, enterprises can significantly improve the quality and efficiency of small-batch PCB assembly, accelerating product commercialization.
Topfast – Your Trusted One-Stop PCB Solution Expert
Company Profile:
Founded in 2008, Topfast is a leading PCB manufacturer with 17 years of industry expertise. We specialize in providing comprehensive circuit board solutions from design to production. With our strengths in small-batch manufacturing and rapid prototyping, we have established long-term partnerships with clients across various industries.
Core Advantages:
- Professional Technical Capabilities
- Experienced Team: Core management and technical personnel each possess over 20 years of PCB industry experience
- Advanced Equipment: Continuous investment in world-class production and testing equipment
- Quality Assurance: Strict compliance with IPC standards and certifications, including UL, RoHS, and ISO9001
- Comprehensive Product Portfolio
- High-End PCBs: HDI boards, heavy copper boards (up to 10oz), high-frequency/high-speed boards
- Specialized Processes: Semiconductor test boards, rigid-flex boards, backplanes
- Full-Service Support: End-to-end solutions from design consultation to mass production
- Industry Application Expertise
Successfully serving:
✓ Communications (5G base stations, optical modules)
✓ Medical Electronics (monitors, imaging equipment)
✓ Industrial Controls (PLCs, HMIs)
✓ Automotive Electronics (ADAS, BMS)
✓ Aerospace (navigation systems) - Customer Value Proposition
- Rapid Response: 24/7 technical consulting from expert teams
- Flexible Production: Quick-turn prototyping with MOQ of 1 piece
- Comprehensive Service: One-stop solutions from DFM analysis to after-sales support
As your reliable PCB partner, Topfast remains committed to innovation, delivering exceptional quality and professional services to ensure customer success. We look forward to collaborating with you to advance progress in electronics manufacturing.