Multiple factors, including board material, number of layers, dimensions, process complexity, production quantity, and special requirements influence the cost of a PCB (Printed Circuit Board). How can you control the budget effectively while ensuring quality under reasonable demands?
Table of Contents
1. PCB Material Selection
The choice of PCB material is fundamental to both performance and cost. Different materials vary significantly in price:
- FR-4 (Epoxy Fiberglass): Most common, low cost, suitable for most consumer electronics.
- Aluminum Substrate: Excellent heat dissipation, used in LED lighting and power modules, 20%-50% more expensive than FR-4.
- High-Frequency Materials (e.g., Rogers, Teflon): Used in 5G, radar, and other high-frequency applications, costing 5-10 times more than FR-4.
- Flexible PCBs (FPC): Bendable, used in wearable devices, higher cost.
Recommendations:
- For general applications, prioritize FR-4; opt for specialized materials only for high-frequency needs.
- Aluminum substrates can replace some heat sinks, reducing overall system costs.
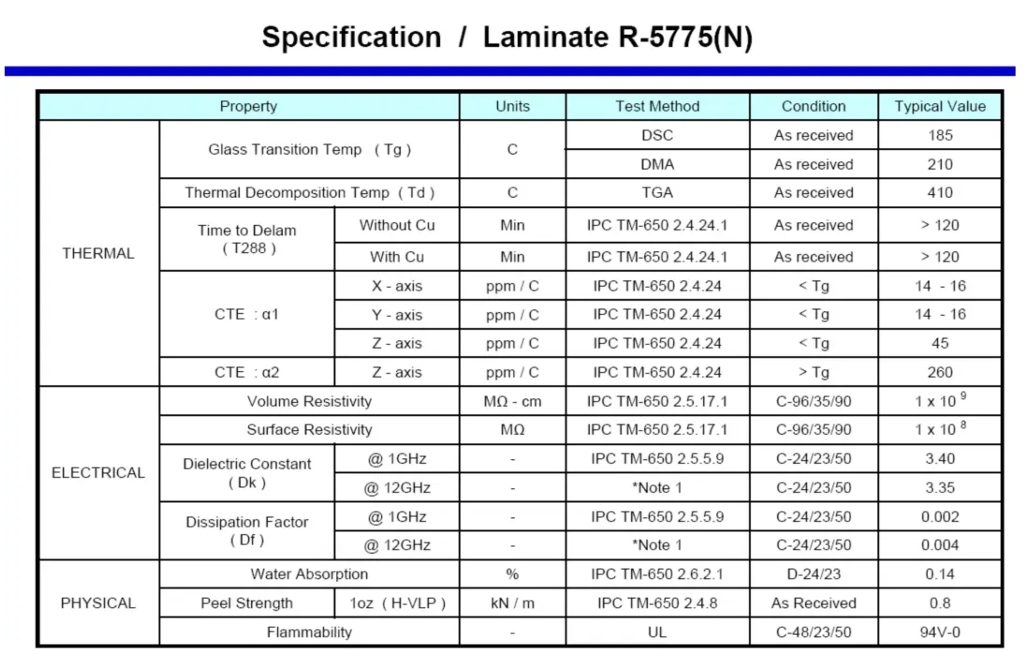
2. Number of PCB Layers
The number of layers directly impacts manufacturing difficulty and material usage—more layers mean higher costs:
- Single-Layer: Cheapest, suitable for simple circuits (e.g., remote controls).
- Double-Layer: Best value, ideal for most consumer electronics (e.g., smart home devices).
- 4+ Layer Multilayer Boards: Used in complex circuits (e.g., motherboards, communication equipment), with each additional two layers increasing costs by 30%-50%.
- HDI (High-Density Interconnect) Boards: Use microvia technology for smartphones and high-end electronics, costing more than standard multilayer boards.
Recommendations:
- Use double-layer boards whenever possible; add layers only when necessary.
- Optimize routing to reduce via counts and lower processing difficulty.
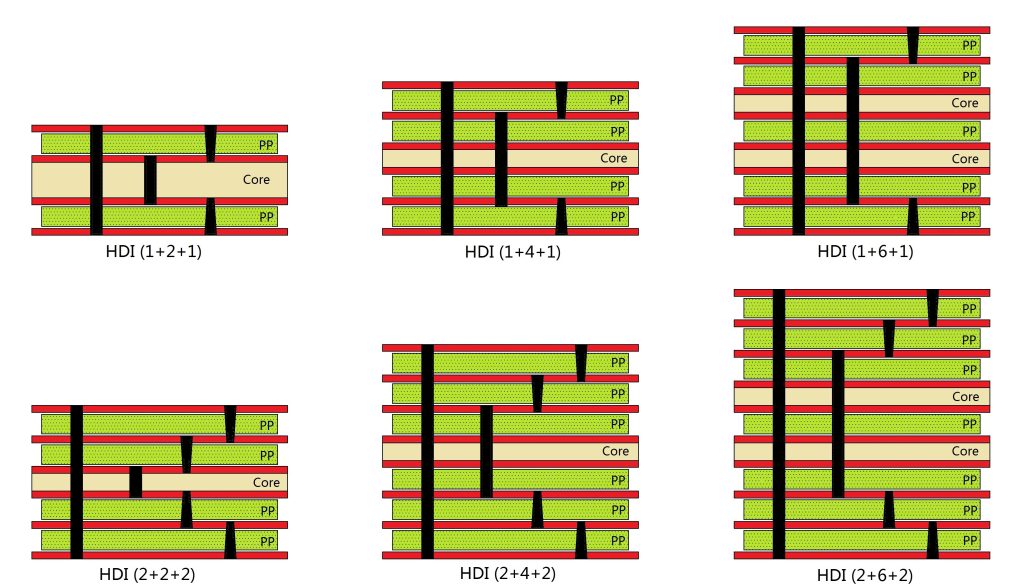
3. PCB Dimensions and Shape
Size and shape affect material utilization and processing costs:
- Standard Sizes (e.g., 10cm×10cm): Higher panel utilization, lower cost.
- Large or Irregular Shapes: May require panelization or special cutting, increasing material waste and processing fees.
- Panelization Design: Multiple small PCBs combined into one panel for production can reduce costs but require V-CUT or breakaway tab considerations.
Recommendations:
- Use standard sizes unless special layouts are required.
- For small-batch production, panelization improves material efficiency.
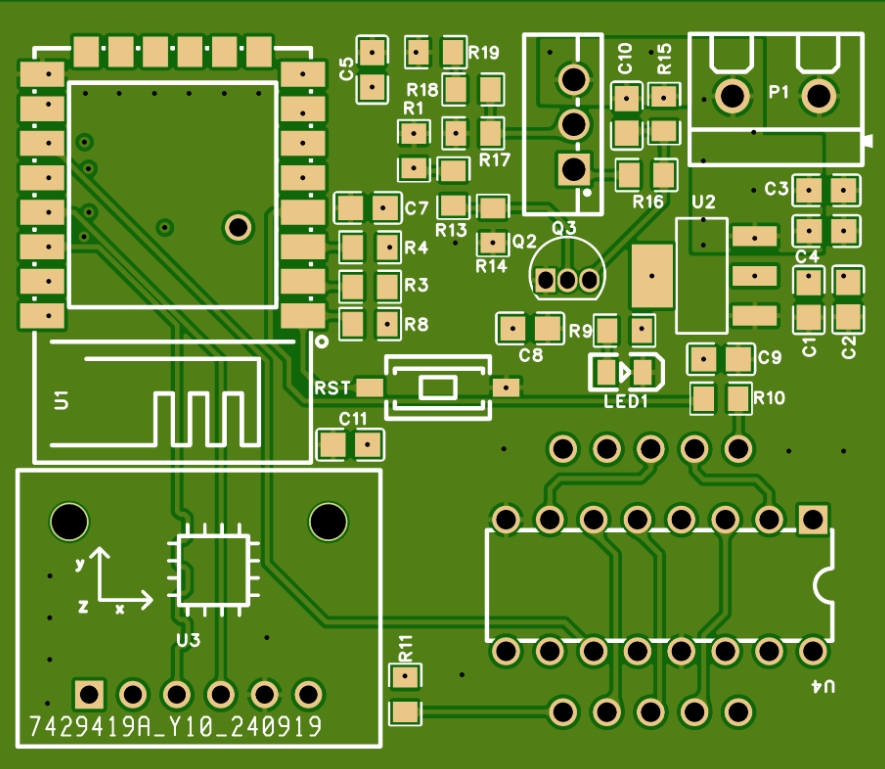
4. Surface Finish Process
The surface finish affects solderability and durability, with varying costs and performance:
Finish | Cost | Applications |
---|---|---|
HASL (Hot Air Solder Leveling) | Lowest | General consumer electronics |
ENIG (Electroless Nickel Immersion Gold) | Higher | High-precision soldering (e.g., BGA packages) |
OSP (Organic Solderability Preservative) | Low | Short-term storage products |
Immersion Silver | Medium | High-frequency signal applications |
Recommendations:
- Choose HASL or OSP for general applications; use ENIG for high-reliability needs.
- Avoid overusing premium finishes unless necessary.
5. Production Quantity
PCB costs are heavily influenced by order quantity—higher volumes lower unit costs:
- Prototyping (1-10 pieces): High per-unit cost due to limited分摊 of engineering and tooling fees.
- Small Batch (50-100 pieces): Unit price drops by 30%-50%.
- Mass Production (1000+ pieces): Economies of scale reduce marginal costs, with unit prices potentially 60% lower.
Recommendations:
- Start with small batches for design validation before mass production.
- Negotiate tiered pricing with manufacturers for better discounts.
Conclusion
PCB costs are determined by material, layer count, dimensions, surface finish, and production volume. To optimize costs:
- Select the right material: Use FR-4 for general applications; reserve specialized materials for high-frequency needs.
- Optimize layer count: Prefer double-layer boards; add layers only when essential.
- Standardize size and shape: Minimize special processing requirements.
- Choose appropriate surface finishes: Balance performance and cost based on soldering needs.
- Leverage bulk production: Validate designs with small batches before committing to large orders.
For accurate quotes, submit Gerber files to multiple PCB manufacturers for comparison and select the best cost-performance solution.
About Topfast
Established in 2008, Topfast is a leading PCB design, manufacturing, and assembly provider with 17 years of experience. As a one-stop PCB solution supplier, we specialize in rapid prototyping and small-batch production services.