TOPFAS is a professional and reliable one-stop PCB solution provider specializing in Rapid Prototyping and Low Volume Manufacturing, Topfast has won wide acclaim in the market for our high quality and on-time delivery of products. We will continue to focus on customer satisfaction and become a trusted PCB service provider with “high quality” and “fast delivery”.
Our products include Flexible PCB, Rigid PCB, Rigid-flex PCB, HDI PCB, High-Frequency PCB, High-Speed PCB, Metal PCB, Ceramic PCB, and so on, to meet the needs of customers. Our products are widely used in communication, medical equipment, industrial control, power supply, consumer electronics, aerospace, automotive industry, and other fields. All of our products are IPC-rated and have passed UL, ROHS, and ISO9001 certifications.
Flexible Printed Circuit Boards, often referred to as FPCs or Flex PCBs, are a major innovation in the field of PCB assembly and PCB manufacturing, and play a very important role in the manufacture of electronic products. Our Flexible PCBs have excellent thermal stability, which is essential for applications that require attention to temperature variations. They can withstand a wide range of temperatures without affecting their electrical performance, even in extremely cold environments, or high-temperature environments, flexible PCBs are less prone to mechanical failure, so they are suitable for harsh environments and applications that require frequent movement.
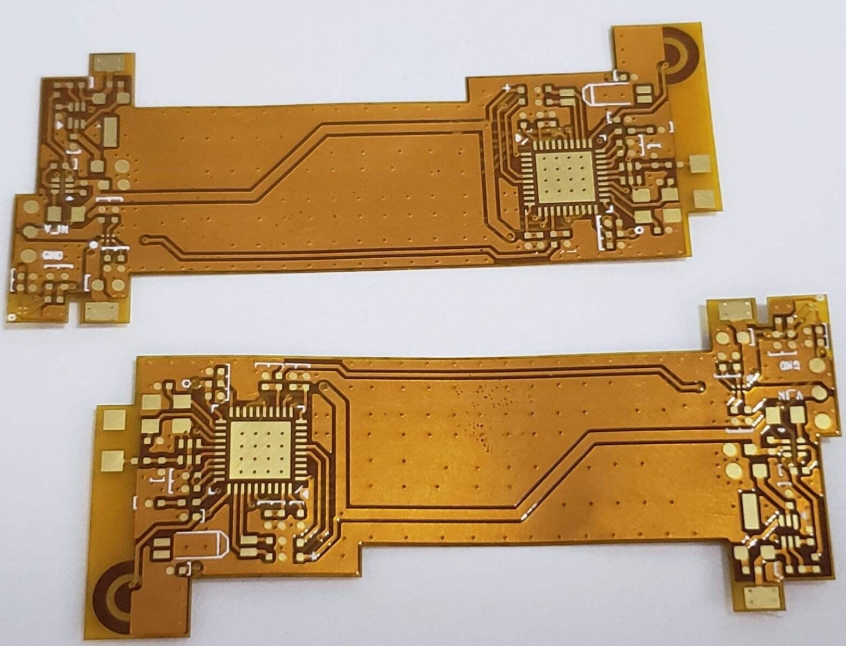
Flexible Printed Circuit Board Plating Precautions
1, FPC plating pretreatment
After the coating process, the copper conductor surface is susceptible to adhesives, ink pollution, high-temperature process may also trigger oxidation discoloration. In order to obtain good plating, it is necessary to remove these pollutants and oxidized layer, and clean the conductor surface. Part of the pollutants and copper conductor bonded tightly, mild cleaning agent is difficult to work, so often use a specific strength of alkaline abrasives and with the brush grinding treatment. The pretreatment cleaning process has a significant impact on the characteristics of FPC, PCB manufacturers need to strictly control this link for the subsequent plating process to lay a solid foundation.
2, FPC plating layer thickness control
The plating process, plating metal deposition rate, and electric field strength are closely linked to the electric field strength by the shape of the circuit pattern and electrode position relationship. In the production of manufacturers based on product design requirements, precise control of the thickness of different parts of the plating layer, in general, the narrower the wire, the sharper the end, the closer to the electrode, the higher the electric field strength, the corresponding part of the plating layer is thicker. To meet the diverse requirements of electronic products on the performance of FPC.
3、FPC Plating Stain Response
Just finished plating PCB plating may appear, the surface rinse solution is not enough, residual plating solution, after a period of slow chemical reaction, the surface is prone to stains, dirt, and discoloration, flexible FPC due to the texture of the soft, uneven, the solution is easy to accumulate in the depressions and react to the discoloration, to avoid this situation, we must ensure that adequate rinsing and drying process. Strict implementation of the relevant operations in the production process, to prevent product quality defects due to appearance problems, enhance the overall quality of the product image, and enhance market competitiveness.
4, FPC hot air leveling
Hot air leveling from the rigid PCB lead-tin coating technology, because of the simplicity of being used in the FPC, the operation is to dip the circuit board vertically into the molten lead-tin bath after hot air blowing off excess solder, but the FPC conditions are harsh. If you do not take measures, FPC is difficult to dip into the solder, needs to be sandwiched between the titanium steel mesh plate operation, and the surface should be pre-cleaned and coated with flux. At the same time, hot air leveling is easy to make the solder from the end of the cover layer drilled underneath, especially in the bond strength is low when more frequently. Polyimide film absorbs water easily, and evaporation of water during hot air leveling can cause the cover layer to blister and flake off. In the hot air, leveling must do a good job of drying moisture management, follow the operating specifications to ensure the smooth progress of the process, reduce the defective rate of the product, reduce a lot of bar, and improve production efficiency.
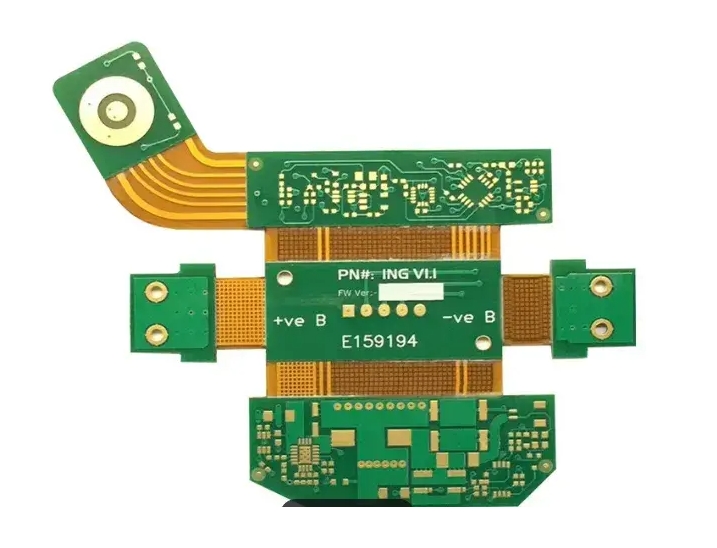
Topfast continuously introduces new types of equipment, and new technologies and adopts high-quality materials to ensure the quality of PCB products, and has professional technicians to provide pre-design consulting and technical support, so that customers can be more worry-free. Our goal is to become a leading PCB solution provider in the electronics industry, providing first-class products and services and is committed to becoming a trusted partner of our customers.