The electronics industry employs various PCB assembly processes to meet diverse design requirements.
Table of Contents
Surface Mount Technology (SMT)
Surface Mount Technology (SMT) is a highly efficient method for mounting electronic components directly onto a printed circuit board (PCB). Due to its advanced automation capabilities, this innovative approach has primarily supplanted traditional through-hole technology. SMT not only reduces manufacturing costs but also significantly enhances overall product quality.
SMT components are characterized by their smaller size than their through-hole counterparts, owing to either smaller leads or, in some cases, no leads. This feature facilitates a higher assembly density, accommodating more components on a given substrate area. The parts may feature short pins, various lead styles, flat contacts, solder balls (BGAs) matrices, or terminations directly on the component body.
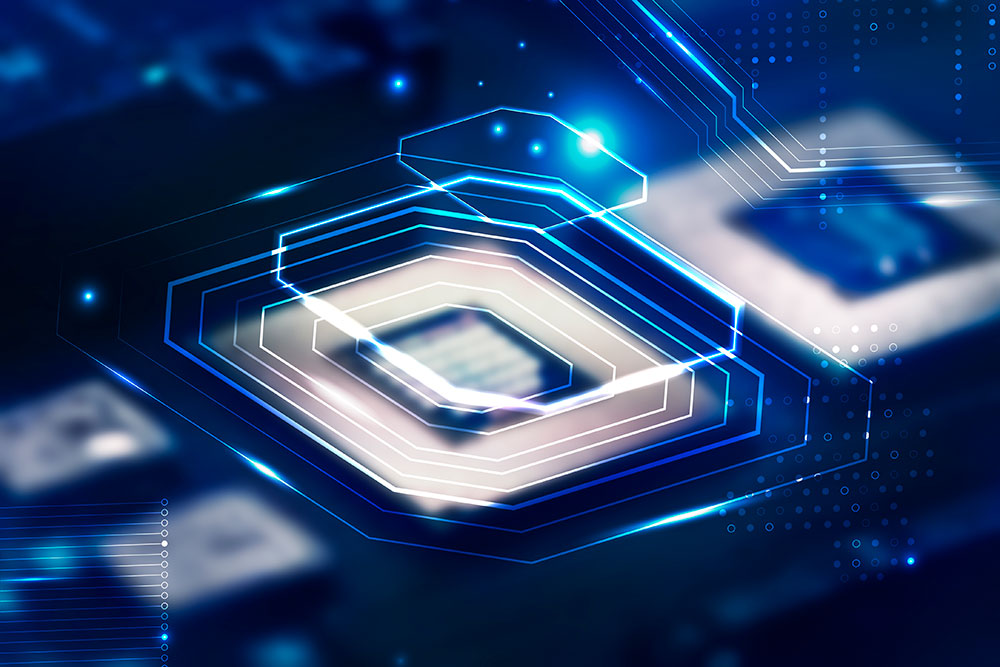
One of the critical advantages of SMT is its widespread use in the electronics industry, which is attributable to its high-speed assembly process, remarkable accuracy, and reliable outcomes. Automated pick-and-place machines play a pivotal role in the SMT process, capable of accurately placing thousands of components per hour.
The benefits of SMT extend beyond its compact design and increased assembly density. It also contributes to improved electrical performance due to the shorter leads inherent in SMT components. Additionally, the reduction in manufacturing costs and improved overall quality are significant factors bolstering the continued dominance of SMT in the ever-evolving tech landscape.
However, it’s essential to acknowledge that SMT has its challenges. Assembly complexity, potential component damage, and limited repairability are notable drawbacks. Nevertheless, these challenges have not diminished the pivotal role of SMT in the electronics industry, where its speed, accuracy, and reliability remain indispensable factors in driving technological advancements.
Through-Hole Technology (THT)
Drilling holes on a printed circuit board (PCB) and inserting electronic component leads into them. Soldering them to the pads, on the other side, is a durable method of assembling parts. This type of Assembly is referred to as through-hole technology (THT). This process establishes a permanent and mechanically stable connection between the component and the board, making THT an optimal choice for applications demanding high reliability and durability.
THT excels when components must endure substantial mechanical stress or operate in challenging environments. Components mounted using THT can withstand high temperatures and vibrations, making this assembly method particularly suited for applications in rugged industrial settings.
THT’s essential advantage lies in its ability to handle high-power components effectively. This feature positions THT as an ideal choice for power electronics applications where reliability and robustness are paramount. Furthermore, the straightforward nature of the THT process adds to its appeal, rendering it a cost-effective option for manufacturers seeking efficiency without compromising on quality.
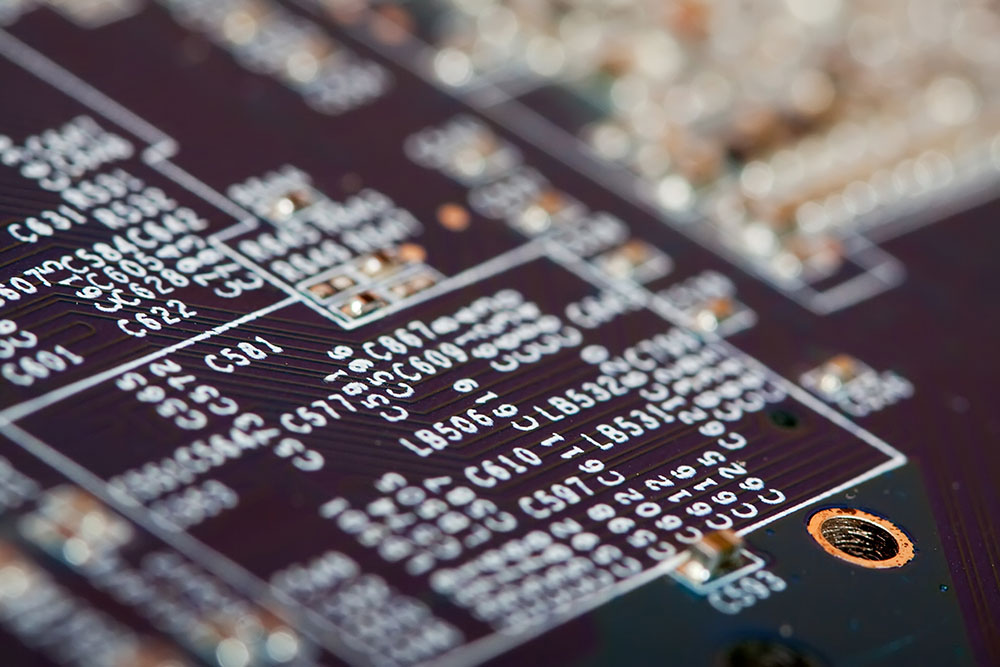
The THT process involves meticulously placing component leads into pre-drilled holes, ensuring a secure and enduring connection. This reliability has contributed to the sustained use of THT in various industries, mainly where resilience to harsh conditions is non-negotiable.
While advancements in Surface Mount Technology (SMT) have led to a gradual shift in industry preferences, THT remains indispensable for applications where mechanical stability, stress resistance, and reliability are non-negotiable. Its straightforward implementation and ability to handle high-power components ensure that Through-Hole Technology remains vital in the diverse landscape of PCB assembly methodologies.
Mixed Assembly
Mixed Assembly stands as a strategic approach in the electronics industry, encompassing a process where both Surface Mount Technology (SMT) and Through-Hole Technology (THT) components coexist on the same printed circuit board (PCB). This hybrid method emerges as a practical solution when design requirements necessitate the unique advantages of SMT and THT.
The integration of SMT and THT components in mixed Assembly is challenging. The differing assembly processes for SMT and THT components require careful consideration and meticulous planning to ensure a seamless coexistence on the identical PCB. Despite these challenges, the benefits derived from mixed Assembly are significant, making it a widely adopted practice in various applications.
One of the critical advantages of mixed Assembly is the potential for improved overall performance. By strategically leveraging the strengths of both SMT and THT components, designers can optimize the functionality of the PCB to meet specific performance criteria. This approach allows greater flexibility in accommodating diverse component requirements within a single electronic system.
Additionally, mixed Assembly enables a higher assembly density, combining the space-saving advantages of SMT with THT’s mechanical stability and reliability. This contributes to more compact device designs and enhances the electronic system’s overall efficiency and functionality.
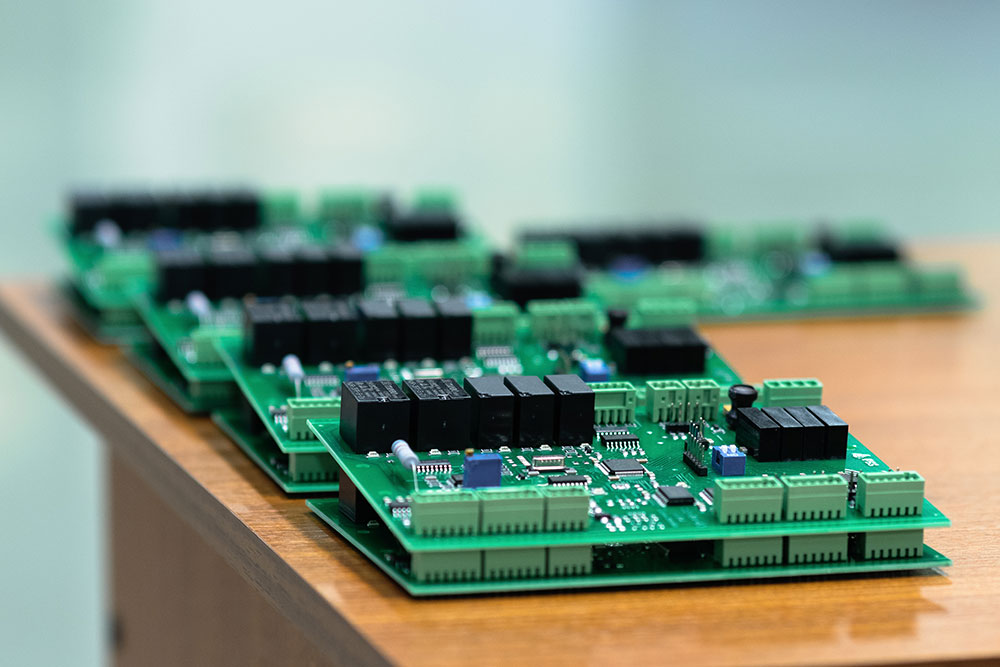
Moreover, mixed Assembly often results in cost savings. By utilizing THT’s cost-effective nature alongside SMT’s automation benefits, manufacturers can balance efficiency and economic viability. This makes mixed Assembly an attractive option in scenarios where achieving the desired performance, density, and cost-effectiveness is paramount.
In summary, mixed Assembly is a versatile and adaptive solution in the electronics industry, allowing designers and manufacturers to harness the strengths of SMT and THT components for optimal performance, efficiency, and cost-effectiveness in a single printed circuit board.
Ball Grid Array (BGA) Assembly
A Ball Grid Array (BGA) represents a sophisticated surface-mount packaging technique extensively employed for integrated circuits, particularly for mounting devices like microprocessors. The distinctive feature of BGA packages lies in their ability to provide more interconnection pins than conventional dual in-line or flat packages, revolutionizing the landscape of integrated circuit packaging.
Soldering in BGA devices demands high precision, typically achieved through automated processes like computer-controlled reflow ovens. During this intricate process, the device is meticulously placed on a PCB with copper pads arranged in a pattern matching the solder balls on the BGA. Subsequently, the Assembly undergoes heating in a reflow oven or an infrared heater, which melts the solder balls. Surface tension is crucial in ensuring the molten solder maintains the package’s alignment with the circuit board at the correct separation distance. As the solder cools and solidifies, it forms reliable connections between the device and the PCB.
BGA packages offer a multitude of advantages over high lead-count packages. The design provides high density, minimizing the footprint of the integrated circuit on the PCB. Furthermore, BGAs exhibit low thermal resistance and low-inductance leads, contributing to enhanced performance, particularly at high speeds. Utilizing the entire bottom surface of the device, instead of just the perimeter, enables more efficient use of space and interconnection points.
The advent of BGA packages addresses a significant challenge encountered in packaging integrated circuits. As pin counts increased and spacing between pins decreased in traditional packages like pin grid arrays and dual-in-line surface mount packages, the risk of accidentally bridging adjacent pins with solder grew. BGA emerged as a solution, offering a compact package for integrated circuits with many pins while mitigating the soldering challenges associated with closely spaced pins.
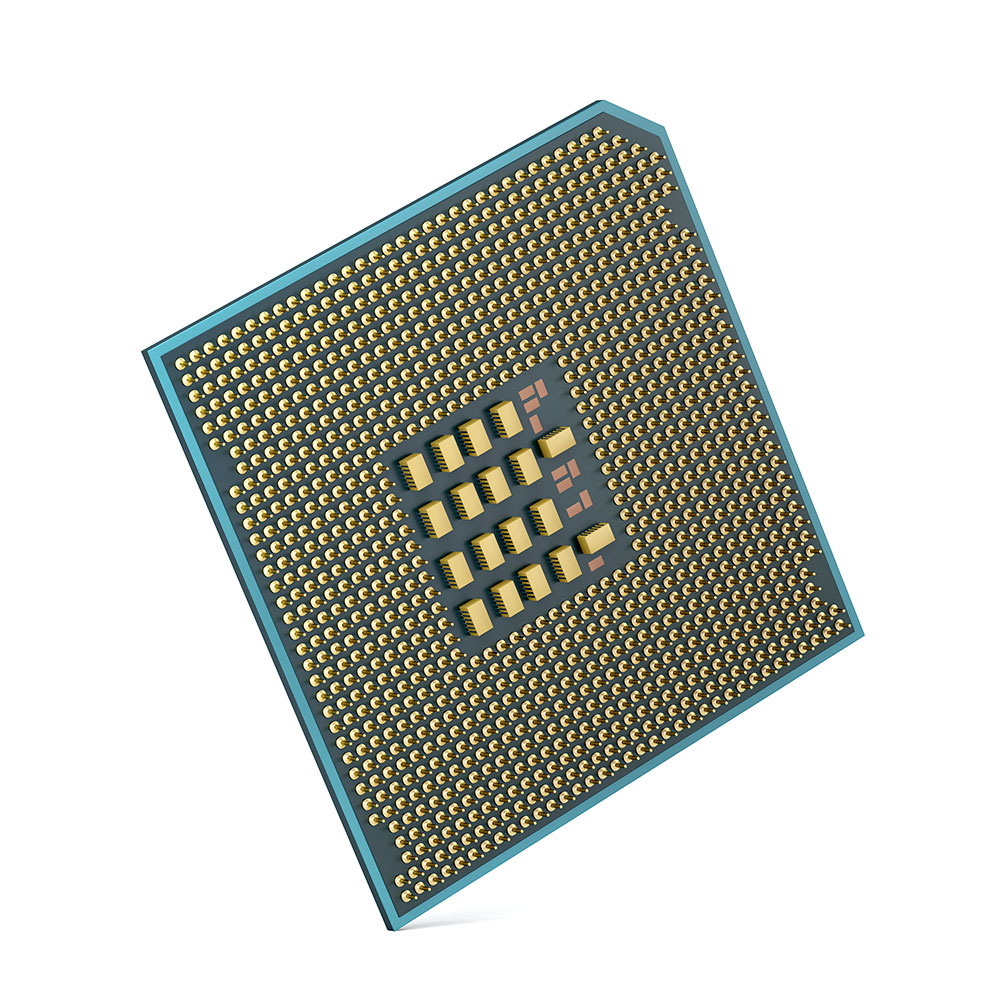
In conclusion, the diverse landscape of PCB assembly processes reflects the dynamic nature of the electronics industry. Surface Mount Technology (SMT) remains dominant, offering efficiency and compact design despite challenges. Through-hole technology (THT) persists in applications requiring robust connections and high reliability. Mixed Assembly strategically combines SMT and THT, optimizing performance and cost-effectiveness. Ball Grid Array (BGA) Assembly addresses high pin-count challenges, providing efficient, compact packaging for integrated circuits. Each process contributes to developing advanced electronic devices, emphasizing the industry’s adaptability and innovation.