PCB and PCBA are two essential components in the electronics industry. An acronym that you might have come across is “PCB.” It stands for “Printed Circuit Board”. On the other hand, “PCBA” is an acronym for “Printed Circuit Board Assembly.” The primary distinction between PCB and PCBA is that PCB refers to a bare circuit board that lacks any electronic components. At the same time, PCBA is a fully assembled and operational board that contains all the required electronic components to function correctly.
Modern electronic devices rely on PCBs as the basis for their operation. These boards provide mechanical support and electrical connections for the various electronic components. Typically made from laminate materials like fiberglass or composite epoxy, PCBs feature conductive pathways that link different board sections.

PCBAs are assembled on top of an existing PCB, and these boards are complete with all the essential electronic components, making them fully operational and ready to perform their intended functions. The parts are mounted on the board using surface mount technology (SMT) or through-hole technology (THT).
PCB refers to a circuit board lacking electronic components, whereas PCBA is a fully functional board with all the required electronic components to function as intended.
Table of Contents
When Do you need PCB, and When a PBCA
If you’re seeking to develop an electronic product, finding a reliable Printed Circuit Board Assembly (PCBA) manufacturer is essential. Conversely, suppose your goal is to prototype an electronic product. In that case, it becomes crucial to engage a manufacturing facility capable of producing a circuit board to serve as the initial sample for your project.
In Electronic Prototyping
- PCB: In the early stages of product development, you may require only the bare PCB without any components. This practice is common when developing prototypes to assess the form and fit of the board.
- PCBA: Once you move beyond the prototyping phase and want a functional prototype, you’ll need the PCB populated with electronic components. Testing the overall functionality of your electronic device is crucial.

Mass Production:
PCB: In large-scale manufacturing, prioritizing consistency and efficiency is crucial. Initially, you may produce a batch of bare PCBs, which can be stored and assembled as needed, streamlining the production process.
PCBA: As demand increases, you’ll transition to mass assembly. PCBA involves populating the bare PCBs with electronic components, soldering them, and conducting quality checks. PCBA constitutes the final step before packaging and distribution.
Extra tests required for PCBAs
As you may have understood, the assembled circuit (PCBA) contains a printed circuit board (PCB). The difference between these terms implies that one lacks any components (PCB). At the same time, the PCBA is the final product, the motherboard with all the necessary parts and sometimes the required software.
A PCB (printed circuit board) is much easier to produce as it requires no assembly. A PCBA is a more intricate device than a PCB. This process includes affixing multiple components and soldering the connections in an oven.
We create additional tests for the PCBA and the ones performed on individual components and the printed circuit board. These other tests are customized to ensure optimal performance. The following are some of the extra tests necessary for PCBA:
Functional Testing: Functional testing for a PCBA involves applying power to the assembly and observing its response to inputs or stimuli. This critical step verifies that the PCBA performs its intended functions, ensuring its overall functionality and reliability.

In-Circuit Testing (ICT): In-Circuit Testing (ICT) is essential for detecting defects like shorts, opens, and variations in resistance or capacitance. Specialized equipment tests individual components while still on the PCB, comprehensively assessing the assembly’s integrity.
Automated Optical Inspection (AOI): Automated Optical Inspection (AOI) utilizes cameras and image recognition algorithms to identify visual defects and verify correct component placement on the PCB. This test is crucial for ensuring the PCBA’s adherence to design specifications.
X-ray Inspection: X-ray inspection penetrates the PCB to reveal hidden solder joints and internal connections. This test is vital for verifying soldering quality and assessing the integrity of complex PCBA structures.
Thermal Profiling: Thermal profiling assesses the PCBA’s thermal performance during operation. Manufacturers ensure the assembly remains within specified thermal limits by measuring temperature profiles under various conditions, preventing overheating and potential failures.
Environmental Stress Testing: Environmental stress testing evaluates the PCBA’s resilience to harsh conditions such as temperature extremes, humidity, and vibration. This simulation of real-world operating conditions ensures the assembly’s durability and reliability.
Burn-In Testing: Burn-in testing involves operating the PCBA under high-stress conditions for an extended period. This process helps identify potential early failures and ensures the PCBA can withstand prolonged usage without compromising performance.
Electromagnetic Compatibility (EMC) Testing: EMC testing verifies that the PCBA doesn’t interfere with other electronic devices and is not susceptible to external interference. This assessment is crucial for meeting regulatory standards and ensuring proper functioning in diverse environments.
Functional Safety Testing: It examines the PCBA under various fault conditions to ensure it meets specified safety requirements. This test provides confidence in the PCBA’s reliability and safe operation in critical applications.
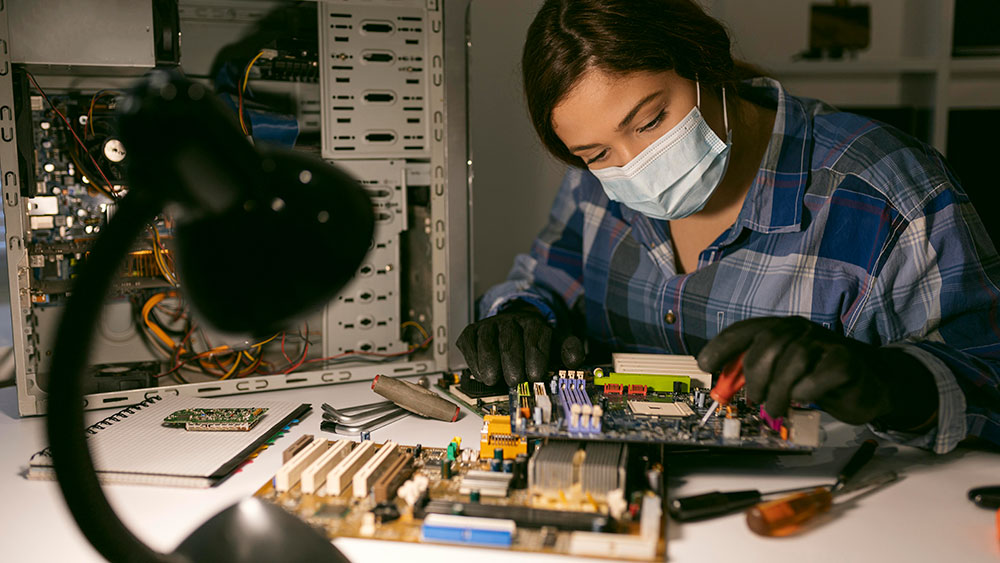
It is imperative for individuals working in the electronics industry to differentiate between PCB and PCBA. This understanding holds significant importance. While a PCB serves as the foundation, a blank canvas with the potential for various applications, a PCBA represents the culmination of the manufacturing process—a fully assembled and functional circuit board ready for implementation in electronic devices.