Table of Contents
Detailed Analysis of Custom PCB Unit Cost: From Design to Mass Production
1. Impact of Substrate Selection on PCB Cost
The type of PCB substrate directly affects manufacturing costs. The base material is the foundation of a PCB and accounts for a significant portion of its cost. Common substrates include FR-4, high-frequency materials (e.g., Rogers), and flexible substrates (e.g., polyimide). FR-4 is widely used due to its cost-effectiveness, while high-frequency or specialty materials are more expensive. Prices vary depending on quality, brand, and specifications.
Copper Foil: As the key conductive material, the amount and cost of copper foil are closely related. Copper foil comes in various thicknesses—thicker foils can handle higher currents but at a higher cost.
Other Auxiliary Materials: These include prepreg, solder mask, and legend ink, which play essential roles in ensuring PCB performance and quality.
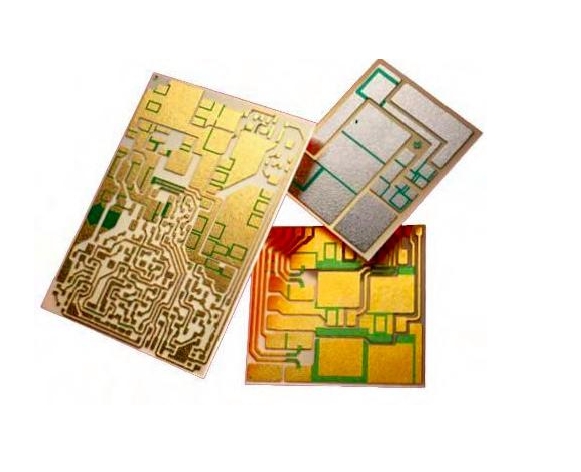
2. Relationship Between PCB Layer Count and Cost
Single-layer PCBs are the least expensive, while multilayer PCBs (e.g., 4-layer, 6-layer, or higher) are significantly more costly due to their complex manufacturing processes. Additional layers require more lamination, drilling, and plating steps, increasing expenses.
A professional engineering team must optimize schematics and routing to generate Gerber files that meet production requirements. Complex multilayer high-speed PCB designs incur higher costs, whereas simple single/double-layer designs are more affordable.
Even with the same materials and processes, manufacturing difficulty affects cost. More challenging PCB designs often lead to higher defect rates, further increasing costs.
3. Process Complexity and Special Requirements
Specialized processes such as blind/buried vias, gold plating, and impedance control increase PCB costs. Designers should balance performance needs with cost considerations to avoid unnecessary complexity.
Manufacturing Methods: PCB fabrication can involve fixed die-cutting or punching, with different methods impacting costs.
Production Techniques: Different processes (e.g., gold-plated vs. HASL boards) result in varying costs.
4. Impact of Order Quantity on Unit Price
Mass production significantly reduces per-unit costs by distributing fixed expenses (e.g., tooling and engineering fees). Prototyping or small-batch orders, however, have higher unit prices. Generally, larger order quantities lead to lower per-unit costs.
5. Supplier Selection and Cost Optimization
Different suppliers have varying pricing strategies, technical capabilities, and lead times. Comparing multiple quotes and establishing long-term partnerships can secure better pricing.
Quality Requirements: Customer quality standards directly affect yield rates—higher standards often increase costs.
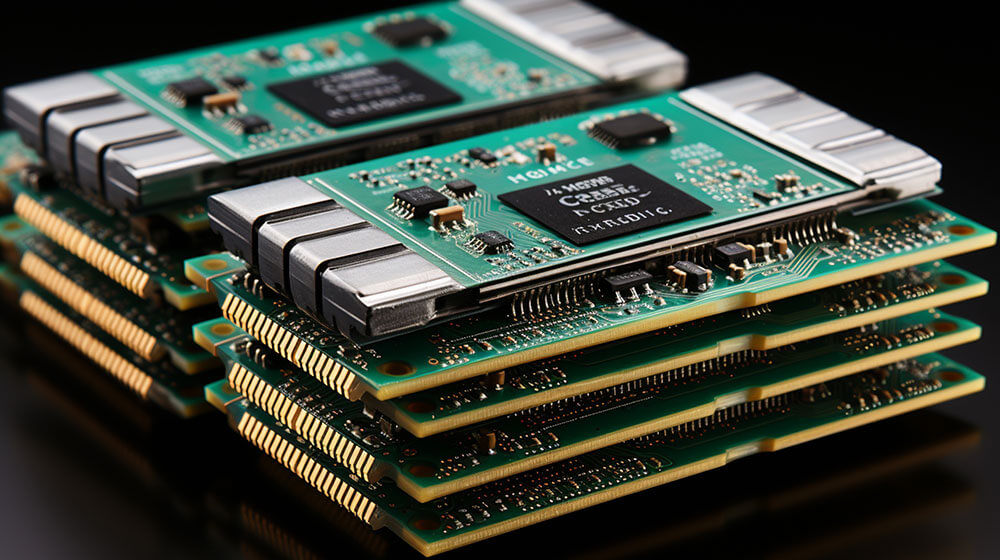
Conclusion
Custom PCB unit costs are influenced by substrate choice, layer count, process complexity, order quantity, and supplier selection. Optimizing designs, selecting cost-effective materials, and bulk purchasing can effectively reduce expenses. It is recommended to communicate requirements with suppliers early in the project to obtain the most cost-efficient solutions.