The special requirements for aerospace PCBs (printed circuit boards) stem from their extreme operating environments and zero-tolerance standards. Unlike consumer electronics, the failure of a spacecraft electronic system can result in hundreds of millions of dollars in equipment damage or even casualties, making it imperative that aerospace PCBs meet nearly exacting technical standards.
Table of Contents
PCBs need to meet four major extreme environmental challenges
1.Temperature extremes
In the space environment, PCBs need to withstand temperature fluctuations between -170 ° C and +125 ° C. This temperature difference is equivalent to the liquid nitrogen cryogenic to high-temperature oven instantaneous switch.
2.Vacuum environment
The near-vacuum environment in space affects the efficiency of heat transfer, but also may lead to the phenomenon of material gas release. This gas release can contaminate delicate optical instruments and even form conductive plasma.
3.Cosmic Radiation
High-energy cosmic rays can trigger the single-particle overturning effect (SEU), leading to errors in stored data or cumulative damage to semiconductor materials.
4.Extreme Mechanical Environment
During the launch phase, PCBs need to withstand vibration acceleration of up to 20G, which is equivalent to sustaining the mechanical impact of a strong earthquake.
It is these stringent requirements that the aerospace PCB, from the choice of materials, process standards, to the test process, are much higher than the norms of consumer electronics, to ensure that during the operation in orbit, to achieves “zero failure” reliability goals.

Aerospace PCB Material Selection
Traditional FR4 materials are unable to meet the demanding needs of the aerospace environment – their lack of thermal stability, mechanical strength, and radiation resistance can lead to circuit failure. Therefore, aerospace PCBs must utilize rigorously proven high-performance materials to ensure long-term reliability under extreme conditions.
1.Polyimide (PI) Substrates
High temperature resistance: can work above 250°C for a long period, and can even withstand 400°C for a short period.
Low Coefficient of Thermal Expansion (CTE): Highly compatible with copper layers, reducing the risk of warpage and delamination caused by drastic temperature fluctuations.
Ultra-low outgassing: Passed NASA ASTM E595 test to ensure that no volatile substances will be released in vacuum to contaminate optical and sensitive devices.
2.Ceramic-filled polytetrafluoroethylene (PTFE)
High Frequency Signal Integrity: Extremely low dielectric loss (Df < 0.002) for millimeter wave radar and satellite communication systems.
Excellent thermal conductivity: ceramic filler enhances heat dissipation to avoid heat buildup in vacuum environments.
High process difficulty: laser drilling and special lamination techniques are required, and processing costs are much higher than ordinary PCBs.
3.Enhanced Plating and Hole Metallization
Thickened Hole Copper (35μm+): Compared to ordinary PCB (20μm), the heat cycle resistance of through-hole is greatly improved.
Pulse plating technology: Ensures a dense and uniform copper layer to avoid micro-cracks and improve long-term reliability.
Rigorous validation standards: Passed 1000 thermal cycling (-55°C↔125°C) tests to simulate years of space temperature alternation environment.
The selection of these materials and process optimization enables aerospace PCBs to maintain stable operation in extreme environments, ensuring the successful execution of space missions.
Aerospace PCB structural design
In the aerospace industry, where every gram of weight loss can reduce launch costs by tens of thousands of dollars, PCB designs must be extremely lightweight while ensuring absolute reliability in extreme environments. This requires innovative structural design methods
1.Ultra-precise impedance control technology
Tough high frequency requirements: impedance tolerance is controlled within ±5% for 40GHz microwave signals to ensure signal integrity of the satellite communication system.
Low-loss transmission: signal loss of <0.3dB/inch is realized by the laser tuning process, which is more than 30% better than the traditional etching process.
Multi-layer structure optimization: Eliminate high-frequency signal crosstalk and improve system EMC performance through precise calculation of dielectric constant and interlayer thickness.
2.Aerospace-grade lightweight design
Ultra-thin substrate application: using a 0.3mm ultra-thin special substrate, 81% weight reduction compared to a conventional 1.6mm substrate.
Shaped structure integration: 3D printing technology is used to manufacture non-standard shaped PCBs, reducing the number of traditional connectors and system complexity.
Space-level BGA optimization: Innovative pad design combined with special solder formulations prevents solder joint fatigue failure in microgravity environments.
3.Mechanically enhanced design
Honeycomb sandwich structure: Based on the spacecraft cabin design concept, the bionic structure is used in key areas to enhance the bending strength.
Dynamic stress analysis: Finite element simulation based on the rocket launch vibration spectrum to optimize the layout of PCB support points.
Miniature vibration-damping design: integrated miniature buffer structure around the key chip to reduce the impact of high-frequency vibration above 10 kHz.
These innovative designs enable modern aerospace PCBs to maintain more than 10 times higher reliability than commercial grade PCBs, despite a weight reduction of more than 50%, perfectly balancing the dual stringent requirements of spacecraft for weight and reliability.
Aerospace-grade PCB Manufacturing Process
The extreme reliability requirements of aerospace electronics have led to several technological breakthroughs in PCB manufacturing processes. These innovative processes ensure that PCBs remain stable for decades in the harsh space environment:
1.High Aspect Ratio Microvia Metallization Technology
A breakthrough in traditional limitations: the development of a horizontal copper sinking process for ultra-high aspect ratio microvias (apertures ≤ 0.15mm) of 10:1 or more.
Plating revolution:
Adopting pulse reverse plating technology to increase the uniformity of copper thickness in the hole by 30%.
Special activation treatment ensures that the bonding force of the hole wall is >1.5N/mm, completely solving the problem of hole wall separation caused by thermal cycling.
Aerospace-grade verification: the process has passed 1000 times of -55℃~125℃ thermal cycle test, especially suitable for high-density interconnect boards with more than 16 layers.
2.Space-level vacuum reflow soldering
Process innovation:
Reflow soldering in 10-³Pa ultra-high vacuum environment
Adopt a gradient temperature rise curve, the temperature rise rate is precisely controlled within 1.5 ℃ / s
Quality breakthrough:
Welded joint bubble rate <0.1%, 90% lower than the conventional process. Thermal stress is reduced by 60%, basically eliminating micro-cracks caused by CTE mismatch. Inspection guarantee: With micro-focus X-ray (<1μm resolution) full inspection of key welded joint.s Adopt an AI algorithm to automatically identify welding defects, detection rate>99.99%.
3.Aerospace-specific surface treatment
Selective gold plating process:
The thickness of the nickel layer in the contact area is 3-5μm, and the thickness of the gold layer is 0.05-0.1μm.
Non-contact area is treated with OSP, which reduces the quality and ensures the reliability of welding.
Atomic Layer Deposition (ALD) protection:
20nm aluminum oxide film deposited on critical circuit surfaces
Increases PCB radiation resistance by more than 10 times
These process breakthroughs reduce the failure rate of modern aerospace PCBs to the 0.001PPM (parts per million) level, which translates to a less than 1% probability of failure over 20 years of in-orbit operation. Each process is certified to NASA ECSS-Q-ST-70-38C and other aerospace standards to ensure that it meets the most demanding space mission requirements.
The Tough Tests of Aerospace PCBs
Before an aerospace-grade PCB can be put into service, it must pass a series of “extreme challenge” reliability tests that simulate the harshest operating conditions in the space environment to ensure that the board is foolproof during its service in orbit.
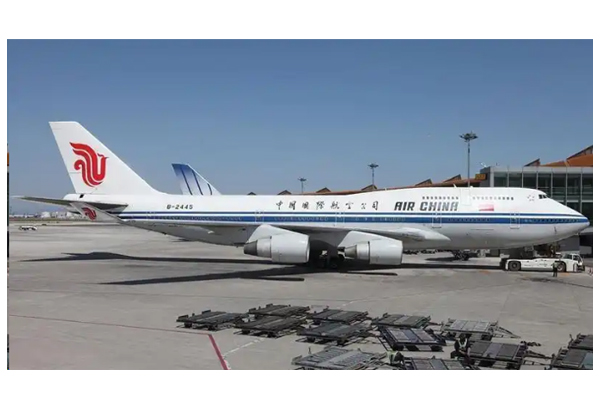
1.Thermal Vacuum Environment Test (TVAC)
Test conditions:
Vacuum: ≤10-⁶ Torr (simulated near-Earth orbit vacuum environment)
Temperature cycling: -170 ℃ to +125 ℃ (lunar surface level extreme temperature difference)
Number of cycles: ≥500 (equivalent to 5 years of orbital operation)
Validation Objective:
Material coefficient of thermal expansion (CTE) match
Gas release rate ≤ 0.1% (NASA ASTM E595 standard)
Stability of dielectric properties under a vacuum environment
2.Radiation resistance test
Radiation environment simulation:
Total Ionizing Dose (TID): 100krad (Si) (equivalent to 10 years of GEO radiation)
Single particle effect (SEE) test: Heavy ion linear energy transfer (LET) ≥80 MeV-cm²/mg
Key indicators:
Functional failure threshold >50krad
Single particle overturning (SEU) incidence <10-⁹ error/bit-day
Components with radiation hardened design (RHBD) need additional verification.
3.Mechanical environment test
Vibration test:
Random vibration: 20-2000Hz, Power Spectral Density (PSD) 0.04g²/Hz (equivalent to rocket launch stage load)
Sine Scan: 5-100Hz, 20g peak acceleration.
Shock Test:
Semi-sinusoidal shock, 1500g peak acceleration, duration 0.5 ms (simulates inter-stage separation shock)
Acceptance Criteria:
No visible damage to the structure
Electrical performance fluctuation <5%
Resonance frequency shift <10
4.Other special tests
Microgravity environment test:
Simulate weightlessness by parabolic flight
Verify the fatigue resistance of solder joints
Atomic oxygen erosion test:
For Low Orbit (LEO) applications
Exposure to a 5-year equivalent dose of atomic oxygen flow
These tests follow the most stringent aerospace standards (e.g., NASA-STD-8739.3, ECSS-Q-ST-70-60, etc.), and failure to meet any of the tests means that the PCB is not flight-qualified. With such a stringent testing system, the reliability of aerospace PCBs reaches a 99.9999% (6 nines) level, ensuring the successful execution of on-orbit missions.
Aviation-grade circuit board precision assembly process
The assembly of circuit boards for avionics equipment is a key manufacturing process to ensure flight safety, and its process is far more stringent than the production standards for ordinary electronic products. The following is a standardized workflow for avionics circuit board assembly:
1.Aerospace-grade component screening and pre-processing
Military grade component screening:
Strictly follow the MIL-PRF-38535 Class K standard.
100% aging screening (168 hours @125℃)
The deviation of key parameters is controlled within ±0.1%.
Special pre-treatment process:
Secondary enhancement of the pin plating treatment
Vacuum baking and dehumidification (48 hours @ 125°C)
X-ray inspection for internal structural integrity
2.Aerospace-specific PCB design and verification
Multi-physical field co-design:
Signal/power integrity analysis using HyperLynx
Thermal simulation optimization using FloTHERM
Structural mechanics simulation to ensure vibration resistance
Design verification standards:
Passed DO-160G aerospace environmental test standards
Meet IPC-6012ES Class 3 reliability requirements
Tolerance of impedance of key signal lines is controlled within ±3%.
3.Highly reliable and precise assembly process
Aerospace grade welding process control:
Adoption of selective laser welding system (accuracy ±25μm)
Real-time thermal imaging to monitor the welding temperature profile
Nitrogen protected environment (oxygen content <50ppm)
Quality Assurance System:
Automated Optical Inspection (AOI) 100% coverage rate
3D X-ray to detect internal defects in solder joints
Flying probe test network connectivity
4.Enhanced environmental adaptability treatment
Three-proof coating process:
Selection of MIL-I-46058 compliant form-fitting coatings
Robot precision coating (thickness control 50±5μm)
UV curing to ensure the density of the coating
Mechanical reinforcement measures:
Fixing of key components with adhesive (high temperature resistant epoxy resin)
Installation of anti-vibration mounting structure
The assembly process strictly implements the AS9100D aviation quality management system, and complete traceability records are established for each link to ensure that the product can still maintain excellent reliability under extreme aviation environments. The entire process, from raw material entry to finished product shipment, goes through more than 200 quality inspection points, and the defect rate is controlled to less than 0.1PPM (parts per million).

Precautions for precision assembly of aerospace grade circuit boards
1.Environmental control specifications
Clean room environmental standards
Air cleanliness: Class 10000 (ISO 14644-1 standard)
Temperature and humidity control: 22 ± 1 ℃ constant temperature, 40 ± 3% RH constant humidity
ESD protection: the establishment of a complete electrostatic protection system (in line with ANSI/ESD S20.20 Class 0 standards)
Special environmental control
Sensitive device storage: nitrogen protection cabinet (O2 content ≤ 50ppm, dew point ≤ -40 ℃)
Welding environment: local micro-positive pressure clean work area (differential pressure ≥ 5Pa)
2.Key process control
Component pre-treatment
Dehumidification: vacuum baking at 125℃ for 48 hours (humidity sensitive level 1-3)
Surface treatment: low temperature plasma cleaning (power 300W, processing time 90s)
Device screening: 100% X-ray inspection of BGA devices (resolution of 0.5μm)
Precision welding process
Positioning system: laser-assisted high-precision alignment (±5μm)
Solder paste printing: stencil thickness 80±2μm, tension ≥35N/cm²
Temperature control: ten temperature zones reflow soldering, real-time temperature curve monitoring (sampling rate of 10Hz)
3.Quality Assurance System
Inspection standard
AOI inspection: fully automatic optical inspection (defect recognition rate ≥ 99.95%)
X-ray inspection: 3D-CT scanning (voxel resolution 0.8μm)
Destructive analysis: metallographic section analysis per batch (≥5 samples)
Reliability verification
Temperature cycle: -65℃~150℃ (1000 cycles, conversion time <1min)
Vibration test: 20-2000Hz random vibration (PSD 0.1g²/Hz)
Environmental test: 85℃/85%RH (2000 hours accelerated aging)
4.Special process requirements
High-density interconnect process
Micro-component assembly: 01005 components, micro-dispensing glue (glue dot diameter 150 ± 10μm)
Fine pitch BGA: 0.3mm pitch special mounting system (accuracy ±3μm)
Thermal management: nanosilver paste thermal conductivity (thermal conductivity ≥ 5W/mK)
Mechanical reinforcement program
Bottom filling: low viscosity epoxy resin (fluidity ≤ 30s)
Connector fixing: mechanical locking + laser welding composite process
Edge treatment: carbon fiber reinforced wrapping (bending strength ≥500MPa)
5.Traceability management
Process data management
Full process parameter record (data retention period ≥15 years)
HD image archiving of key processes (resolution 4K@60fps)
Material traceability system (batch number to single piece level traceability)
Personnel qualification management
Operator: IPC-A-610 Class 3 certified
Process Engineer: J-STD-001 Aerospace Specialized Certification
Quality personnel: MIL-STD-883 method training certification
Note: This specification strictly enforces AS9100 Rev D quality management system requirements, which need to be met by all critical processes:
MSA analysis results: GR&R ≤ 8%.
Process capability index: CpK≥1.67
PFMEA risk factor: RPN≤80
First article qualification: 100% dimensional and functional verification
Future Trends
1.Disruptive Manufacturing Technology Breakthroughs
Fourth-generation additive manufacturing technology
Multi-material composite printing: Synchronized precision deposition of dielectric and conductive materials
Topology-optimized structures: Bionically designed shaped circuit boards with up to 65% weight reduction
On-orbit manufacturing capability: direct printing of circuit modules for maintenance in space environment
Intelligent self-assembly technologies
Molecular-scale self-assembled circuits: quantum dots self-aligned with 0.5nm precision
Reconfigurable circuit architecture: Autonomous adjustment of circuit topology according to mission requirements
2.Artificial Intelligence-Driven Design Paradigm Revolution
Cognitive electronic design system
Multi-objective optimization engine: Simultaneous optimization of 12 performance indicators including EMC/thermal/mechanical etc.
Failure prediction AI: Predict potential failure points 2000 hours in advance
Digital Twin Verification: 10^6 reliability simulations in a virtual environment
Autonomous Design Evolution System
Genetic Algorithm Evolution: 15% increase in design performance per generation
Cross-generation knowledge migration: build an intelligent library of over 100,000 design cases
3.Next Generation Core Technology Innovation
Bio-inspired material system
Self-healing smart substrate: 95% conductivity restored within 24 hours after damage
Neuromorphic circuitry: mimics the adaptive ability of the biological nervous system
Quantum Interconnect Technology
Terahertz transmission channel: realizing interconnect density of 100Gbps/cm²
Photon-electron fusion: optical interconnect loss reduced to 0.1dB/cm
Intelligent Energy Management
Micronuclear cell integration: directly embedded in radioisotope energy cells
Intelligent power consumption adjustment: Autonomous adjustment of power supply strategy according to the mission phase
4.New Paradigm of Aerospace Electronics Reliability
Extreme environmental adaptability
Deep space level protection: withstanding 10^6 rad radiation dose
Wide temperature range: -200℃~+300℃ stable operation
Intelligent management of the whole life cycle
On-orbit health monitoring: real-time transmission of 500+ status parameters
Predictive maintenance: over 99.99% accuracy rate
Industry Outlook:
With the integration of quantum computing, nanotechnology, artificial intelligence, and other cutting-edge technology breakthroughs, aerospace electronics is undergoing revolutionary changes. It is expected that by 2030:
Circuit board power density will exceed 50W/cm³
On-orbit service life extended to 20 years
System failure rate down to the order of 10^-9/hour
These breakthroughs will directly support manned Mars missions, lunar base construction, and other major space projects, and promote mankind to enter a new era of “interstellar civilization”. Each technological innovation is a manifestation of the infinite pursuit of cosmic exploration and the pinnacle achievement of human engineering wisdom.