Why are circuit boards (PCBs) mostly green? Green soldermask is widely used mainly because it effectively protects the wiring on the board from foreign short-circuiting and also covers the copper wires to enhance their robustness. In addition, not only does green soldermask exist in the market, but there are also other options, such as red and black, but green is favored for its unique advantages. So, what is the difference between other colors of soldermask ink besides green?
Table of Contents
Why Are PCBs Predominantly Green?
I. Fundamental Functions of Solder Mask and Color Selection
- Core Protective Functions
- Physical protection: Prevents accidental circuit breaks
- Soldering control: Precisely defines soldering areas to avoid bridging
- Environmental protection: Blocks moisture, dust, and chemical corrosion
- Technical Differences Between Colors
- Green series: Best overall performance (precision, viscosity, curing)
- Dark series: Black/blue carries conductive impurity risks
- Light series: White/yellow has higher viscosity, affecting HDI wiring
II. Technical Drivers for Green as Industry Standard
- Precision Manufacturing Advantages
- Supports 6 mil ultra-fine line design (critical for IC test boards)
- 30-40% lower optical alignment error (vs dark masks)
- Superior via filling capability (15% better per Taiyo Ink data)
- Production Process Compatibility Production Stage Green Advantage Data Support Yellow Room Ops Optimal visual contrast 40% faster inspection SMT Process 98 %+ optical recognition <0.5% AOI false alarms Curing Specific wavelength absorption 20% faster curing
- Material Property Advantages
- Ideal viscosity (12-14Pa·s for HDI boards)
- No conductive additives (vs cobalt-blue/carbon-black)
- Excellent thermal stability (no gas release at 300℃)
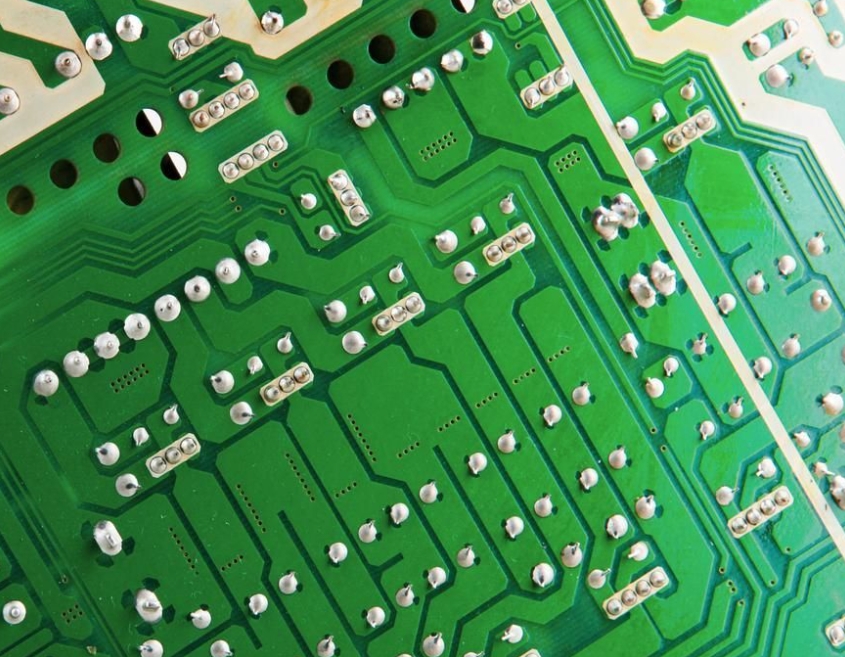
III. Economic Logic of Market Selection
- Cost Structure Analysis
- Economies of scale: 65% global market share
- Procurement cost: 8-12% cheaper than black
- Line conversion: Saves $1,500 per color change
- Industry Chain Synergy
- Optimized inspection equipment: Green-specific algorithms
- Adapted maintenance systems: Industry standard
- Inventory advantage: 3-5 day lead time
IV. Exceptions for Special Applications
- Premium Brand Choices
- Black PCBs: ASUS/MSI premium strategy (+15-20% cost)
- Gold PCBs: Luxury electronics branding
- Emerging Material Applications
- Ceramic substrates: LED/sensor field (12% YoY growth)
- Transparent substrates: Flexible electronics
V. Key Misconception Clarifications
- Performance Neutrality
- Electrical characteristic variation <2% (all colors)
- Thermal performance depends on the base material (FR-4 vs ceramic)
- Selection Decision Matrix

Industry Evidence: Data from a major motherboard manufacturer shows black PCBs, while enhancing brand image, result in:
- 0.7% higher return rate
- 25% increased inspection cost
- 3-day longer lead time