Difference between 2-layer PCB and 4-layer PCB
2-layer and 4-layer PCBs are two of the most commonly used PCBs in the technical field. There are many other options for the number of PCB layers, such as single-layer, multi-layer, or even 6- or 8-layer PCB boards. However, 2-layer and 4-layer PCB boards are widely used in most prototypes or technical equipment because of their ease of installation. When you build a circuit board, it is very important to consider the factors affecting the overall price of the design. The cost structure mainly depends on parameters like dielectric material, number of layers, physical dimensions, and trace parameters.
Table of Contents
Comparison of the advantages and disadvantages of 2-layer PCBs and 4-layer PCBs
Analysis of 2-Layer PCB Pros and Cons
2-layer PCBs are widely used in electronic design due to their cost-effectiveness, lightweight nature, and simple structure, though they may have limitations in high-performance applications.
Advantages
- Cost Efficiency
Production costs are significantly lower than 4-layer designs, making them ideal for budget-sensitive projects. - Faster Design and Production Cycles
Simplified structure reduces design complexity, shortens development time, and minimizes manufacturing errors. - Suitable for Mass Production
Offers better cost-performance ratios and production efficiency for large-volume orders requiring quick turnaround.
Disadvantages
- Limited Component Capacity
Lower routing space and component density compared to 4-layer PCBs may restrict complex functionality. - Signal Speed Constraints
Electrical performance may be inadequate for high-frequency/high-speed signals, necessitating multilayer designs. - Size and Flexibility Limitations
Often requires a larger board area to accommodate routing, increasing device size, and reducing suitability for compact products.
Application Recommendation
Best for low-complexity, cost-driven projects. Multilayer designs are preferred for high-performance or high-integration scenarios requiring optimized signal integrity and space utilization.
Analysis of 4-Layer PCB Pros and Cons
4-layer PCBs excel in applications demanding superior signal integrity, power handling, and space efficiency due to their advanced architecture.
Advantages
- Complex Design Support
Additional routing layers enable high-density component placement and high-speed signal transmission. - Enhanced Signal Quality
Dedicated power/ground planes reduce noise and improve signal integrity, benefiting even simple designs. - Higher Power Capacity
Optimized power distribution suits high-current applications where 2-layer PCBs face thermal/current limitations. - Mechanical Robustness
Multilayer lamination provides greater durability for high-vibration or extreme-temperature environments.
Disadvantages
- Higher Cost
Increased material usage and complex manufacturing processes lead to substantially higher costs. - Design Complexity
Requires expertise in signal integrity, impedance matching, and extended design validation cycles. - Longer Lead Times
Additional lamination and drilling steps prolong production compared to 2-layer PCBs. - Challenging Repairs
Internal layer faults are harder to diagnose and repair than in 2-layer boards. - Supplier Limitations
Not all manufacturers can meet the precision requirements for 4-layer production.
Application Recommendation
Ideal for high-speed digital circuits (e.g., microprocessors, communication devices), high-power modules, or space-constrained designs. 2-layer PCBs remain the economical choice for cost-sensitive projects with modest performance needs.
Comparison of 2-layer and 4-layer PCB stacked structures
2-Layer PCB Stackup Structure
- Basic Construction
- Simple dual-layer design with copper layers on both top (Layer 1) and bottom
- Copper thickness is adjustable per design requirements
- Straightforward structure with low development difficulty
- Routing Characteristics
- Doubles the routing area compared to single-layer PCBs
- Interlayer connections are achieved through vias
- All electrical connections require implementation
4-Layer PCB Stackup Structure
- Core Architecture
- FR4 or glass epoxy core as central layer
- Prepreg sheets are bonded to both sides of the core
- Four copper layers laminated under high pressure
- Interconnection Methods
- Outer copper layers connected via soldering
- Inner layers are interconnected through precision drilling and plating
- Solder points are located on the outermost copper layers
- Process Features
- Requires thermo-compression bonding for layer adhesion
- Prepreg materials ensure robust top-bottom layer integration
- Manufacturing complexity is significantly higher than 2-layer PCBs
Layer Count Identification
- Determine PCB layers by conductor pattern count
- Standard 4-layer PCBs show four distinct conductor layouts
- Layer quantity corresponds to visible conductor patterns
Design Complexity Comparison
- 2-Layer PCBs
- Relatively simple routing schemes
- Suitable for basic circuit designs
- Shorter development cycles
- 4-Layer PCBs
- Substantially increased routing complexity
- Requires multilayer signal integrity considerations
- Extended development timelines
Key Differences Summary
Characteristic | 2-Layer PCB | 4-Layer PCB |
---|---|---|
Structural Complexity | Low | High |
Routing Space | Limited | Significantly Expanded |
Manufacturing Process | Simple | Complex (Requires Lamination) |
Interlayer Connection | Via Connections | Multilayer Interconnects (Vias+Buried Vias) |
Development Cycle | Short | Relatively Long |
Application Scenario | Simple Circuits/Cost-Sensitive Projects | Complex Circuits/High-Performance Applications |
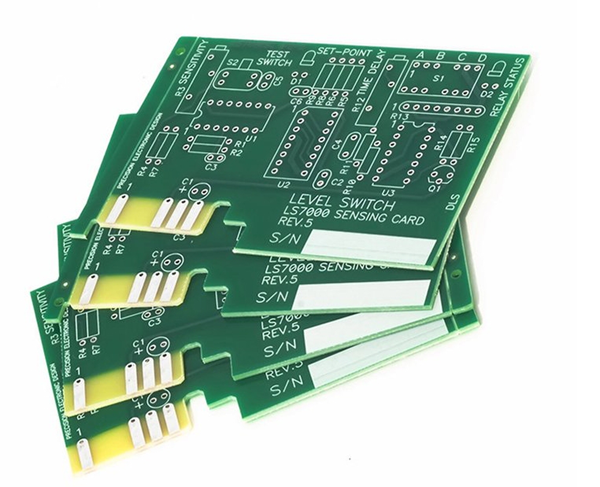
2-Layer vs. 4-Layer PCB Functional Characteristics Comparison
Functional Characteristics of 2-Layer PCBs
- Signal Transmission Advantages
- No propagation delay issues, more direct signal paths
- Fewer interlayer transitions ensure better signal integrity
- Simplified microstrip routing implementation on ground planes
- Recommended Applications
- Simple circuits with strict timing requirements
- Low-frequency signal processing applications
- Cost-sensitive projects without complex routing needs
Functional Characteristics of 4-Layer PCBs
- Signal Processing Features
- Potential impedance matching challenges from a multilayer structure
- Observable signal propagation delay phenomenon
- Requires special attention to signal integrity and crosstalk control
- Structural Advantages
- Dedicated ground and VCC planes ensure stable power distribution
- Inner layer insulation materials enhance thermal resistance
- Multilayer structure effectively suppresses EMI interference
- Recommended Applications
- Systems tolerant to signal delays
- High-reliability equipment requiring long-term stable operation
- Complex digital circuits and high-speed signal applications
Key Functional Comparison
Feature | 2-Layer PCB | 4-Layer PCB |
---|---|---|
Signal Delay | Negligible | Controllable delay range |
Routing Complexity | Simple and direct | Requires multilayer SI consideration |
Thermal Management | Relies on external cooling | Built-in insulation for better thermal stability |
EMI Suppression | Limited | Excellent multilayer shielding |
Long-term Reliability | Suitable for general applications | Ideal for harsh environments |
Selection Guidelines
- Choose a 2-Layer PCB when:
• Project budget is constrained
• Circuit complexity is low
• Extremely strict signal timing is required - Choose a 4-Layer PCB when:
• High-speed signal processing is needed
• System demands high reliability
• EMI performance optimization required
• Complex power distribution involved
Note: Actual selection should comprehensively consider cost, performance requirements and production cycle. For mixed-signal systems, 4-layer PCBs typically deliver superior overall performance.
2-Layer vs. 4-Layer PCB Cost Comparison
1. Manufacturing Cost Differences
- Price Range:
- 4-layer PCBs are 30%-50% more expensive than 2-layer PCBs
- Primary cost differences stem from complex processes and material requirements
- Cost Drivers:
Cost Factor | 2-Layer PCB | 4-Layer PCB |
---|---|---|
Material Cost | Lower | 40%-60% higher |
Production Process | Simple lamination | Precision lamination + drilling |
Yield Rate | Higher (>95%) | Relatively lower (~85%-90%) |
Equipment Requirements | Standard equipment | High-end lamination equipment is required |
2. Design Cost Comparison
- 2-Layer PCB Design:
- Simpler, more straightforward routing solutions
- Lower engineering expertise requirements
- The design cycle is typically 30%-50% shorter
- 4-Layer PCB Design:
- Requires signal integrity and EMI considerations
- Demands experienced multilayer PCB designers
- Longer design verification cycles
- Design costs may increase 2-3x
3. Performance Value Analysis
While 4-layer PCBs are more expensive, they offer critical advantages:
- Signal Integrity:
- Dedicated power/ground planes reduce noise
- More precise impedance control
- Crosstalk reduction up to 60%-70%
- Enhanced Reliability:
- More even thermal distribution
- ~40% improvement in mechanical strength
- Suitable for long-term heavy-duty operation
4. Cost-Benefit Selection Guidelines
- Choose 2-Layer PCBs when:
✓ Strict project budget constraints
✓ Shorter product lifecycle
✓ Signal rates <50MHz
✓ Annual production volume >100k units - Choose 4-Layer PCBs when:
✓ High-speed signals (>100MHz) required
✓ High product reliability demands
✓ EMI performance optimization is needed
✓ Expected product lifecycle >5 years
5. Industry Application Trends
- Consumer electronics: Prefer 2-layer PCBs for cost control
- Industrial equipment: 60% adopt 4-layer PCBs for reliability
- Communication devices: Over 80% use 4-layer or more
Note: Actual cost variations depend on order quantity, material selection, and manufacturer capabilities. Pilot production is recommended before mass production to verify the cost-performance ratio.
Comparison of 2-layer vs. 4-layer PCB prototypes
1. Innovations in Modern Prototyping Technology
- Digital Design Workflow:
- EDA tools (e.g., Gerber) enable automated design
- Multilayer configurations via parametric software settings
- 2-to-4-layer expansion requires only a stackup definition
Manufacturing Advances:
Process | Traditional | Modern Prototyping |
---|---|---|
Lamination | Dedicated equipment | Standardized rapid systems |
Drilling Accuracy | ±100μm | ±25μm (Laser drilling) |
Lead Time | 2-3 weeks | 24-72h rapid turnaround |
2. Design Complexity Management
- Automation Benefits:
- Impedance calculators auto-optimize trace parameters
- 3D preview visualizes interlayer relationships
- Real-time DRC error correction
- Outsourcing Advantages:
✓ Dedicated rapid prototyping lines
✓ Instant online quoting (<15min avg response)
✓ One-click Gerber/X-file submission
✓ DFM (Design for Manufacturing) analysis reports
3. Prototyping Cost Comparison
- Narrowing Price Gap:
- 4-layer premium reduced from 50% to 20-30%
- Smaller differential for low-volume (5- 10 pcs) orders
Time Cost Alignment:
Service Level | 2-Layer | 4-Layer |
---|---|---|
Standard | 24h | 48h |
Expedited | 8h | 12h |
4. Professional Service Selection
- Ideal Vendor Traits:
- Portfolio with 50+ successful similar projects
- Complimentary design review services
- Multi-format deliverables (incl. 3D STEP)
- ISO9001-certified production facilities
- Prototyping Validation Focus:
✓ 4-layer: Layer alignment precision
✓ 2-layer: Core functionality verification
✓ Both: Basic signal integrity testing
5. Industry Trends
- Startups: 87% outsource prototyping
- Hardware accelerators: Standard rapid prototyping services
- Design firms: Average 40% shorter development cycles
Note: Recommend ≥3 prototype iterations before mass production. Impedance testing and thermal simulation are advised for 4-layer boards. Modern PCB prototyping now makes multilayer designs as accessible as double-layer ones.
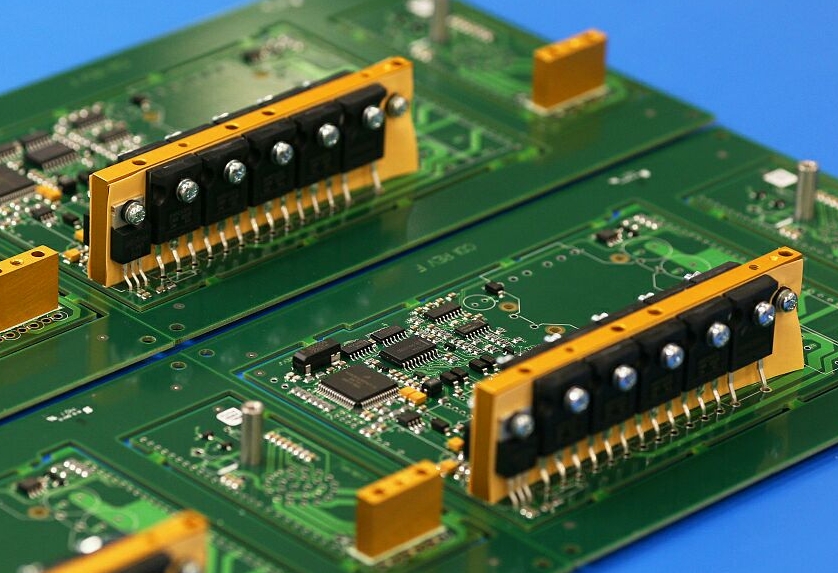
Comparison of key selection factors for 2-layer vs. 4-layer PCBs
1. Space and Functional Density Considerations
- 4-Layer PCB Advantages:
- 40-60% size reduction compared to equivalent 2-layer boards
- Supports 2-3x higher component density
- Inner layer routing frees up surface space for component placement
- Typical applications: Wearables, IoT modules, medical implants
- 2-Layer PCB Use Cases:
✓ Devices with less stringent space constraints
✓ Applications with moderate functional density requirements
✓ Designs requiring maximum board area utilization
2. System Complexity Evaluation
- 4-Layer PCB Suitability:
- Supports high-speed bus layouts (>16-bit)
- Enables mixed-signal integration (digital+analog+RF)
- Dedicated power planes for multi-voltage management
- Typical applications: Industrial controllers, comm modules, premium consumer electronics
- 2-Layer PCB Limitations:
✓ Single-function or low-frequency systems (<50MHz)
✓ Single power voltage designs
✓ Circuits with <100 logic gates
3. Reliability and Lifespan Analysis
Reliability Metric | 4-Layer PCB | 2-Layer PCB |
---|---|---|
MTBF | >100,000 hours | 50,000-80,000 hours |
Thermal Cycling | -40℃~125℃ range | 0℃~70℃ operating range |
Vibration Resistance | MIL-STD-810G compliant | Static applications only |
Typical Lifespan | Industrial-grade 10-15 years | Consumer-grade 3-5 years |
4. Cost vs Development Cycle Tradeoffs
- Cost-Effective Option:
- 35-50% lower BOM cost for 2-layer
- 40% shorter development cycle (2 vs 4 weeks avg.)
- Ideal for: Promotional products, educational kits, proof-of-concept prototypes
- Value Investment Option:
✓ 4-layer reduces post-sale maintenance by 30%
✓ Enables future firmware upgrades/expansion
✓ Recommended for: Flagship products, medical devices, infrastructure
5. Key Decision Parameters Checklist
Evaluate these quantifiable metrics:
- Signal Integrity Requirements:
- Frequency threshold (>100MHz recommends 4-layer)
- Signal rise time (<1ns requires 4-layer)
- Routing Density Needs:
- Vias per cm² (>20 suggests 4-layer)
- Special traces (differential pairs, impedance-controlled)
- Production Considerations:
- Annual volume (<1k units may justify a 4-layer cost)
- Product iteration cycle (rapid iterations favor a 2-layer)
Recommend using a weighted decision matrix. When score differentials are <15%, prioritize a 4-layer for long-term technical flexibility. For mission-critical systems, 4-layer reliability advantages typically deliver better total cost of ownership despite higher initial costs.